In this article we will cover the main types of motors we carry here at T.I.E Industrial. The motor is the heart of every automated motion system. The type of motion you are looking to achieve will dictate the motor needed to bring the motion to life.
Servo Motors
One of the more popular motors you see in today’s motion control systems. Servo motors used in robotics and automation are chosen due to having the following characteristics: fast response speed, high starting torque, wide speed range. The typical servo motor is made up of an electric motor, a position control loop, a velocity control loop, and a current control loop.
Here are the current functions of each loop:
- Position control loop – commands the velocity control loop in order to ensure the motor is rotating into the correct position.
- Velocity control loop – controls the velocity (the amount of rotational velocity of the motor shaft) of the motor.
- Current control loop – prevents the motor from being overloaded by controlling the current of the motor.
Servo motors are chosen more often due to the amount of precision they control when paired with a feedback device such as a control and a servo drive.

Types of Servo Motors
Single Phase (Brushed DC Motor)
These motors are simple in complexity. Within the motor are small magnets looped into the coils and wire within the rotor. These magnets create a magnetic field when the current runs through the coils creating a force that causes the rotor to move. To ensure that the wires do not get tangled up in the process you have the commutator and the conductive brushes.
Despite the name, the brushes are actually pieces of graphite that are then spring loaded to make contact with the commutator of the motors as it spins creating an electric current. The commutator is a round piece with contact points made of metal that are connected to each of the rotor’s coil loops.
Brushed motors provide an economical solution for short-life applications. The downside to this motor is that due to the constant friction of the brushes and the commutator, this motor typically requires more maintenance over a long period of time.
Three Phase (Brushless DC Motor)
Unlike their brushed counterpart, brushless motors have permanent magnets in the actual rotor of the motor. There is no commutator in this motor and instead the electricity is run through the stator. The DC current and their coils interact with the magnetic field caused by the rotor’s magnets which is used to power the stator’s three phases. This allows two motor phases to be active at one time and the alternating between the two motor phases created the magnetic field that cases the rotor to spin.
DC Brushless motors are more complex causing their overall initial expense to cost more than a brushed motor. What makes this type of motor ideal is the decreased need for maintenance. The lack of mechanical contact within the motor means increased heat dissipation and an overall greater electrical efficiency. This makes the brushless DC motor an overall perfect solution for long term cost savings and for applications where the motor is not easily accessible.
Brushless AC Motors
Perhaps the most efficient of the motors is what is known as a permanent magnet synchronous or a PMAC motor. These motors run the current through the strator and have their magnets located in the rotor similar to the DC brushless motor, but that is where the similarities end. The servo drive powers each motor phase differently creating a different result.
Instead of alternating two motor phases at one time like the DC motor, the AC brushless motor constantly has current running through all three phases. The brushless AC runs the current in a sinusoid fashion similar to how an AC supply runs it’s current from a wall outlet. By doing this, the magnetic field becomes more of a net that rotates more smoothly.
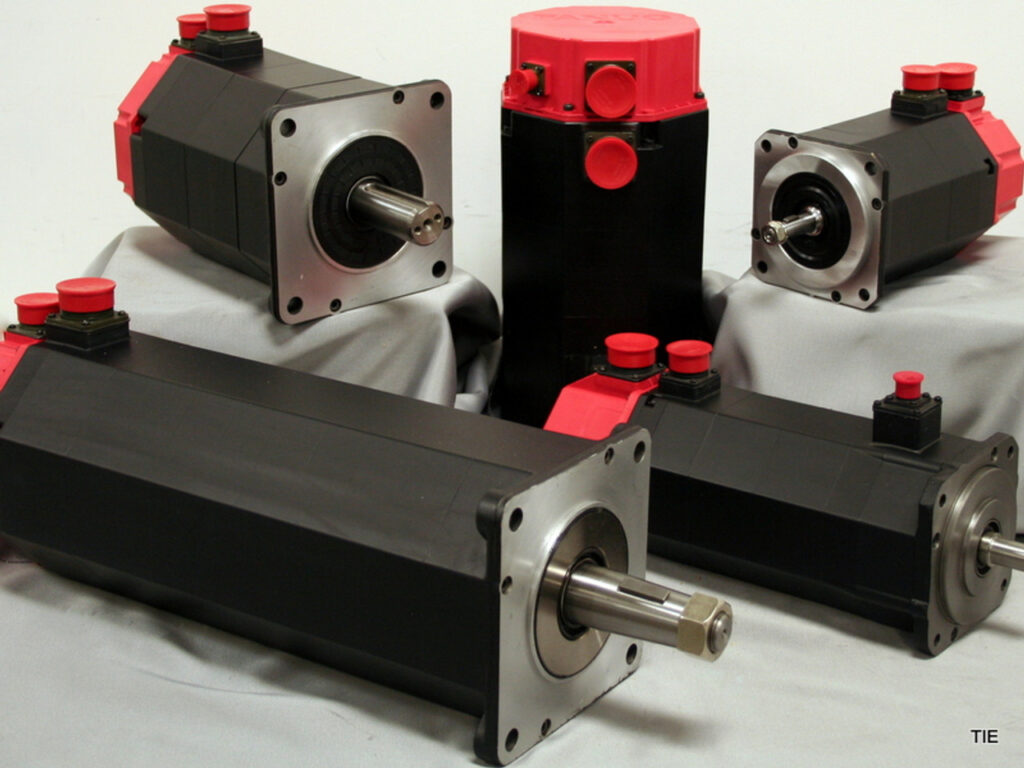
Linear Motors
Linear motors are unique in that they do not involve spinning to get their current. In Linear motors the permanent magnets are laid out in a long track alternating the polarity of each magnet. These motors also include three phases of coils, a rotor and a stator but these coils are housed in a moving carriage. The rotor and stator are flipped and appear above the “track” of magnets. From here the current is pushed through the coils which magnetize the three phases either north or south which pulls or pushes it along the motor track.
These motors are great for applications that need increased precision and speed but in a linear motion. This motion could be oriented either horizontally, vertically or at an angle. A good example of an application that would use a linear motor is an industrial 3D printer.
Spindle Motors
Last but certainly not least on our list is spindle motors. Spindle motors are primarily used for movements or motions that require high RPM’s, fast stopping and starting, and 360 positioning. These motors tend to be more power efficient than their servo counterparts. Operating on either a closed or open loop system, these motors are able to function without an encoder or resolver but can be outfitted with positional feedback and a tachometer if needed. Most common uses for spindle motors are metalworking and machines that work with wood, stone, glass and PVC piping.
Now that you know more about how each motor operates, feel free to check out our motor page to start finding the ideal motor for your application. If you still aren’t sure which motor you need feel free to contact our tech support to walk you through your application to find the correct part. Have a more specific need for an existing application? We can repair your industrial servo motor as well.
Get your Fanuc CNC machine back up and running.
TIE offers same day shipping on more than 100,000 Fanuc CNC parts in stock. We offer a 1 year in service warranty on all parts and repairs.
Shop PartsWas this helpful?
0 / 2