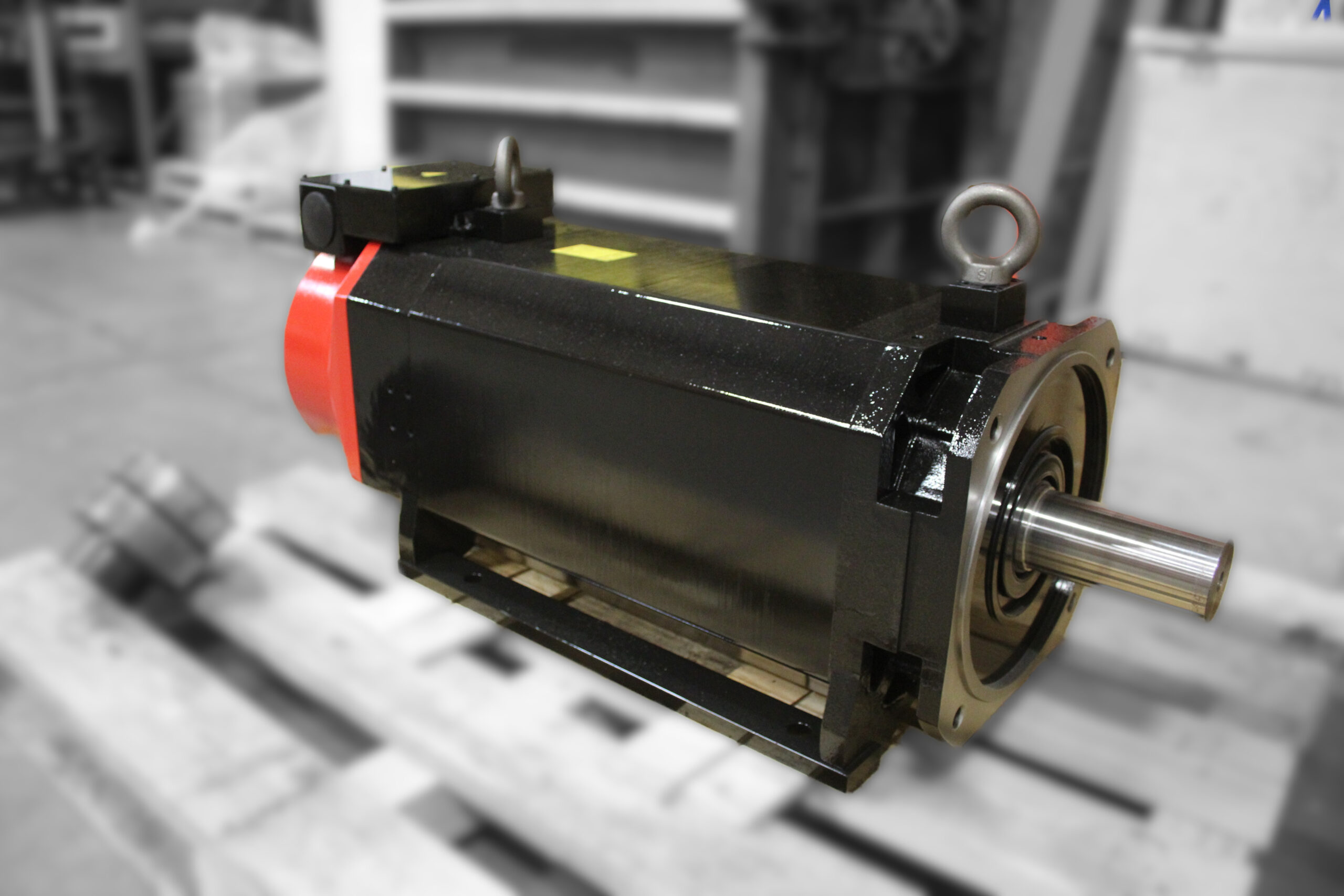
As with any piece of industrial equipment, good maintenance is important for CNC machine tools. Poor maintenance leads to poor performance, needless repairs, and the risk of significant downtime. Also, bear in mind that spindle motors and servo motors are connected to other parts, like a motor sensor, that may cause problems that show up in poor motor performance. This article offers more details on why Fanuc CNC motor maintenance is important and how to make sure that your motors and associated parts perform at their best.
Preventive Maintenance of Your Fanuc CNC Tools Saves Money
This is the main argument for keeping a strict maintenance and cleaning schedule for the various motors in your Fanuc CNC tools. A commercial truck has several subsystems that need regular maintenance. The engine, transmission, brakes, suspension and tires all need regular checkups to avoid premature failure and expensive maintenance. As with that commercial truck, your CNC router, mill, or lathe may come with recommended maintenance intervals for some parts. Or, you may have to create your own schedule using industry best practices or a tip sheet on someone’s Website.
The controllers, power supplies, drivers, spindles, and motors need preventive maintenance. So, while this post focuses on motors, they are part of a system and some of the scheduled maintenance checks should be done along with other routine inspections or maintenance work.
Doing so reduces a few different risks. Unexpected downtime is the most obvious risk. An expensive motor could reach the end of its life sooner than expected, which imposes a significant expense and some early downtime. Losses to parts being worked may impose another cost if the motor doesn’t work as intended.
Recommended Maintenance Checks and Scheduling
If you don’t have a printed cheat sheet for machine maintenance, consider creating one. Whether you create one or not, consider breaking down routine motor maintenance tasks according to how often they should be performed. Here is one scheme to use:
- Daily
- Weekly
- 500 hours (or 3 months)
- 1,000 hours (or 6 months)
- 2,000 hours (or 1 year)
Where do motors fit in? Here are some suggestions from CNC maintenance and repair pros:
Daily
Clean the motor and motor shafts.
Check the machine for unexpected noise or vibration.
Check output voltage stabilizer against specifications.
Watch for signs of overheating.
Monitor your control for any signs of performance deviations.
Weekly
Check cooling fans to be sure they are operating as expected.
Visual inspect motors, drives, and power supplies.
Clean the machine shop.
Inspect the machines for water, oil, or coolant leakage.
Monthly
Clean the fans to prevent dust and dirt buildup.
Check lubricant consumption for possible anomalies.
Inspect pulleys, chains, and conveyors. Tighten or replace if necessary.
Semi-Annually
Inspect and clean the brushes in your DC motors.
On heavily used machines you may want to to annual checks twice a year.
Annually
Run software simulations to evaluate tool performance.
Replace oil filters.
Inspect oil for signs of contamination.
Other CNC tool systems will need maintenance, so why not create a detailed maintenance list covering each type of machine? Create a maintenance log that codifies the checklist you created. These days, you could use specialized software or create an Excel workbook for the shop’s CNC machine tools.
At the very least, this is an easy way to keep any important tasks from being forgotten. Use the above maintenance intervals or others that fit the tool or operating environment. For example, a Fanuc CNC mill that runs almost all day every day will need more preventive maintenance than a mill or router you run an hour or so per day.
Supplemental CNC Motor Maintenance Tips
While taking a look at motors, don’t neglect the parts connected to them. A quick look at shafts, gears, wires, and power lines could tip you off to a problem before it becomes an expensive one. If something seems to be wrong with a motor, it might be one of those connected parts, like a bad motor sensor, so being familiar with their condition can streamline troubleshooting.
Dust, moisture, and grease are a real hazard to a machine tool’s operations. Dust and grease are a hazard for the precise tolerances and movements involved in CNC machining. Moisture is a threat to electronics and computers. Manage those risks by including careful cleaning of the machine shop, the machine exterior, along with individual motor casings, and various surfaces inside the machine.
Prevent Needless Downtime with a Solid Maintenance Plan
Good preventive maintenance practices can’t prevent every problem. If a spindle motor, servo motor, or drive motor should fail, contact the CNC tool experts at Fanucworld to troubleshoot and repair that motor. If the motor is done, or if one of the connected parts needs to be replaced, we have over 100,000 Fanuc CNC and robot parts in stock. Either way, you can count on our CNC repair experts to get your important machinery up and running as quickly as possible.
Was this helpful?
0 / 1