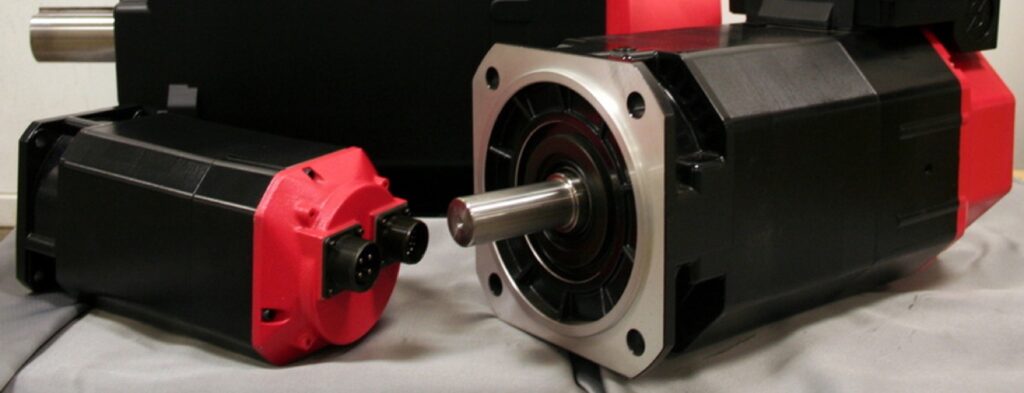
CNC machine downtime can cost thousands in lost productivity—and one of the biggest culprits is spindle motor failure. Today’s machine tool spindles are faster and more complex, and the costs associated with repairs are increasing. Fanuc spindle motor preventative maintenance is key to help prolong the life of your machining equipment.
When you partner with T.I.E. Industrial for spindle motor repair, you gain access to a vast inventory of over 500 AC and DC Fanuc spindle motor components, allowing you to resume operations quickly. Our comprehensive repair process restores motors to OEM specifications, with rigorous load testing to guarantee optimal performance. Backed by a full one-year in-service warranty, we deliver reliable, high-quality repairs to keep your processes running smoothly.
The Impact of Fanuc Spindle Motor Preventative Maintenance
At T.I.E. Industrial, we’ve seen all types of damage, from the drive keys being completely sheared off the shaft to overheating, corrosion, and more. These motors often operate in a dirty environment with severely contaminated bearings, which is the most common cause of spindle failure.
Other causes include:
- Crash or impact damage due to human error
- Lack of lubrication
- Machine vibration
- Programming mistakes
- Misaligned tools
- Incorrectly mounted fixturing
When spindle motor repair becomes necessary, the entire machining process grinds to a halt. Without a functioning spindle, CNC machines can’t perform cutting, drilling, or milling operations. You may scramble to source replacement parts or schedule emergency repairs, but that only adds to the unexpected downtime and expenses.
Regular spindle maintenance can help prevent supply chain disruptions and customer order delays and also provides long-term benefits.
Lower Operating Costs
Preventative maintenance of spindle motors helps identify and handle potential complications before they escalate into costly repairs. You can avoid breakdowns that lead to expensive emergency repairs and production halts by conducting routine inspections, cleaning, and servicing.
A proactive approach also minimizes unplanned downtime and facilitates continuous production and optimizes operational budgets. Over time, the investment in regular maintenance proves to be more cost-effective than reactive repairs.
Boosted Efficiency
Well-maintained Fanuc motors operate at peak performance levels, leading to smoother operations and higher precision in machining tasks. Regular maintenance properly lubricates, aligns, and removes contaminants, which reduces the likelihood of errors and rework.
This efficiency enhances product quality and increases overall productivity, allowing manufacturers to meet deadlines and customer expectations more consistently. Additionally, efficient machinery consumes less energy, contributing to cost savings and environmental sustainability.
Increased Machine Lifespan
Routine maintenance prevents premature wear and tear that shortens the service life of spindle motors. Addressing minor issues early on keeps machines remain functional and reliable over an extended period.
Reducing the frequency of equipment replacements leads to substantial cost savings. Moreover, a longer machine lifespan allows for better capital planning and allocation of resources to other critical areas of the business.
Strengthened Workplace Safety
Safe working environments rely on spindle motors that are in good working condition. Regular inspections and maintenance reduce the risk of sudden machine failures that could endanger operators.
Proactive maintenance protocols help prevent accidents caused by malfunctioning equipment, reducing potential liabilities. A safe workplace also boosts employee morale and productivity, as workers are more confident and focused when operating well-maintained machinery.
Indicators That Spindle Motor Maintenance Is Necessary
Identifying early signs of Fanuc motor failures, such as electrical malfunctions, winding damage, or shaft misalignment, is crucial for preventing expensive downtime and making sure your equipment performs properly.
Promptly managing these problems through regular maintenance prevents inconsistent spindle speeds, excessive runout, and thermal expansion that can lead to poor surface finishes and inaccurate cuts.
Spindle motor issues that require maintenance include:
- Excessive noise or vibration
- Decline in machining precision
- Overheating
- Frequent tool breakages
- Unusual power consumption
Keeping electrical connections secure, lubricating bearings properly, and ensuring alignment prevents unnecessary tool wear, unbalanced loads, and loss of rigidity, all of which impact machining precision and overall efficiency.
In-House Preventative Maintenance of Spindle Motors
Over time, accumulated debris, such as metal shavings and dust, can infiltrate a CNC spindle assembly, leading to:
- Increased friction
- Overheating
- Premature wear of components
Plus, undetected misalignments, wear, or lubrication deficiencies can result in mechanical failure, electrical hazards, and safety concerns. Incorporating general preventative maintenance procedures can uncover these problems so you can correct them before they escalate.
1. Clean Spindle Motors Regularly
Routine Fanuc motor cleaning schedules help CNC equipment operate smoothly and reliably by preventing contamination from metal shavings, dust, coolant residue, and grease buildup. Clean spindle environments contribute to better machining accuracy, as contaminants can adversely affect the precision of the spindle’s movements. Regular spindle cleaning also helps maintain proper heat dissipation, preventing excessive thermal expansion that can lead to misalignment and inconsistent cutting performance.
2. Inspect Equipment Before Operation
Pre-operation checks allow operators to identify potential issues, such as loose fittings, worn components, or fluid leaks, that could compromise safety and efficiency. Addressing these problems early prevents minor defects from escalating into major failures that cause costly downtime and pose safety risks.
Ongoing inspections also keep you compliant with safety regulations and extend the service life of machinery by promoting timely maintenance interventions.
3. Perform Preventative Maintenance Procedures
You can prolong the life of your machine tool spindle motors by adding a few simple maintenance procedures to be performed on a monthly basis:
- Regularly inspect and replace machining fluids to prevent contamination from debris, bacteria, or coolant breakdown, ensuring optimal lubrication and cooling performance.
- Follow manufacturer guidelines when installing or removing a spindle to prevent misalignment, excessive force, or damage to critical components.
- Apply the recommended type and amount of lubricant at scheduled intervals to reduce friction, prevent overheating, and extend the lifespan of spindle bearings.
- Handle spindle bearings with care during maintenance and operation to prevent sudden impacts or shocks that can cause premature wear or failure.
- Use high-quality, properly seated, precisely matched tool holders to minimize runout, enhance machining accuracy, and reduce wear on spindle components.
In addition, conduct monthly vibration analyses using an accelerometer to detect imbalances, misalignment, or early signs of wear that need corrective action.
FAQs About Spindle Motor Preventative Maintenance
Keeping your spindle motors in peak condition means smooth operations and long-term reliability. To help you better understand our services, we’ve answered a few common questions about preventative maintenance, service quality, and turnaround times. Need more information? Reach out today.
How often do Fanuc spindle motors need preventative maintenance?
Maintenance frequency depends on usage and operating conditions, but a general guideline includes daily, weekly, monthly, semi-annual, and annual checks. For example, daily tasks involve cleaning the motor and checking for unusual noises or vibrations, while annual tasks include running software simulations to evaluate tool performance.
What services does T.I.E. Industrial offer for spindle motor maintenance?
We provide comprehensive maintenance services, including thorough inspections, cleaning, component testing, and replacement of worn parts. Our process guarantees motor operation at or above original OEM specifications.
How does T.I.E. Industrial guarantee the quality of spindle motor repairs?
T.I.E. Industrial follows a meticulous 10-step quality checklist for Fanuc motor repairs, which includes disassembly, component testing, cleaning, and precision balancing. Each motor undergoes final testing on a Fanuc control to ensure optimal performance.
What is the turnaround time for spindle maintenance services?
Turnaround times can vary based on the specific service required and motor condition. We strive to minimize downtime and offer rush repair services when necessary.
Was this helpful?
1 / 0