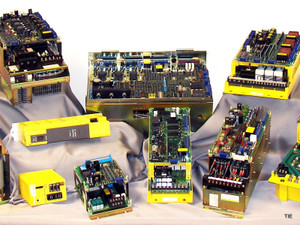
It is almost inevitable that at some point a Fanuc spindle drive or motor within your cnc machine will need servicing. If this happens it is crucial to get your machine back online as quick as possible. One way to reduce machine downtime and expedite your repair is to do a bit of troubleshooting and share what you learned with your spindle drive repair provider.
Sometimes Fanuc CNC parts come in for repair without any information on the problem. This makes it harder for a CNC repair tech to find and fix the problem which increases the amount of downtime for your CNC machine. So, here are some questions to try and answer before seeking repair work on Fanuc spindle drives.
1. Is the problem with your spindle drive intermittent or continuous?
If the problem comes and goes, a quick test may not reveal a problem. If the problem is intermittent, how long are you running the machine between occurrences of the problem? Make note of how long the tool runs before having a problem. If the problem seems to happen at shorter intervals as time passes, that is also important to know.
2. Did the spindle drive’s performance change, and how?
Some failures are sudden, others begin as minor issues and grow worse. It helps to know if the problem appeared suddenly or developed over time. Tell us how long it ran before the problem appeared. Spindle drives can work in some ways so it helps to know if the drive can “orient” itself properly.
3. Are there error codes associated with the problem?
Knowing the specific error code that you see on the Fanuc control will streamline our troubleshooting efforts. The error code, for example, may tell you that the problem is actually with another part. The code will otherwise tell our technician where to start on diagnosing the part when it comes in. What happened just after the error code appeared? And, what happened just before the error code appeared?
4. What Fanuc control is your CNC machine using?
The controller’s may show different error codes or LED indicators in spite of the underlying module, drive, or motor having a specific issue.
5. Does it behave the same way in another machine?
Have you tried switching out the drive with another machine to see if the behavior is the same. This might be a time-consuming test but it will help confirm that the spindle drive is the problem.
6. Have you recently replaced this part?
Sometimes the replacement does have a hidden fault that only shows up after it has to perform in a real manufacturing environment. More often, something connected to that replacement part is the issue.
7. Are you sure the spindle drive is really the problem?
Sometimes when it seems that spindle drives are failing another part is really the problem. For example, wiring and power supplies can affect the drive’s performance even if the part itself is not at all affected. The sensor may also be bad. There are a couple of follow-up questions you can ask if you are not sure the spindle drive is the problem.
Having a CNC machine tool go down is expensive, so help us help you get things running again. The more information about the nature of the problem we have, the easier it is to diagnose and repair your Fanuc CNC part.
Get your Fanuc CNC machine back up and running.
TIE offers same day shipping on more than 100,000 Fanuc CNC parts in stock. We offer a 1 year in service warranty on all parts and repairs.
Shop PartsWas this helpful?
0 / 0