Reshoring of manufacturing goods in the US is on the rise. More and more manufacturing companies are seeing the lasting positive effects of manufacturing automation. Many companies are utilizing robots to do some of the more dangerous and let’s face it dirtier work to help augment their existing workfaces. This change in operations is leading to a variety of positives including the ability to scale with the market’s demand, as well as employee retention, particularly with their highly skilled trade workers. One of the hardest trade workers to find in the current times are welders. Welders, especially welders for automotive manufacturing companies, have industry specific codes and standards they must comply with for each application. Finding employees with this knowledge can be especially challenging. This, along with some other key benefits, has brought most automotive manufacturers to seek the assistance of robotic welders to help meet these production goals.
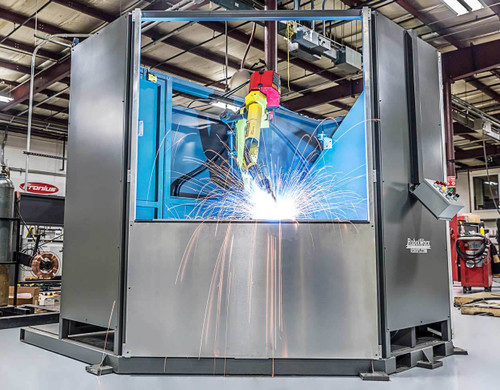
Measure once, cut once
Robots are programmed to complete a task with an extreme level of precision that is difficult for humans to achieve. As we mentioned earlier, there are codes and standards that every weld application must comply with. Welding can be repetitive and let’s face it we are all still human. Robots can perform the same task 24 hours a day with little to no downtime for cleanup or rework. Not only do they perform the same task repeatedly they do it to your exact specified parameters leaving you with a better-quality product with nearly 100% accuracy.
Mistakes can pop up at times for various reasons that can have a significant impact in not only the quality of your product, but the number of materials used to correct an imperfect weld. Some other common mistakes that are solved/avoided by using a robot similar to our Fanuc ARC Mate 100iC/7L could include incomplete penetration, undercutting, over welding and many more. The decrease in waste materials alone can have a significant impact in your profitability.
Robots increase safety in the workplace
It’s no secret that employee safety is important to all employers. The automotive industry has historically had upwards of three times more incidents reported than any other industry. The BLS TED reports that in the past twenty years nonfatal incident rates of over 15 per every 100 full time workers in 2003 to less than 3 per every 100 full time workers in 2018!
Welding robots specifically play a part in the decrease of these numbers by eliminating some very common welding injuries.
These injuries include but are not limited to:
- Welders Eye – caused by radiation damage to your cornea from the UV light on a welding torch.
- Topical burns – Burns caused on the skin from fire, sparks or other flammable material.
- Electrocution – This can be caused by the welder creating a “bridge” between the welding supply and the welding return of the equipment.
Adding robotic welders to your production floor can greatly mitigate these safety risks and help you keep your workers safe while still maintaining quality assurance.
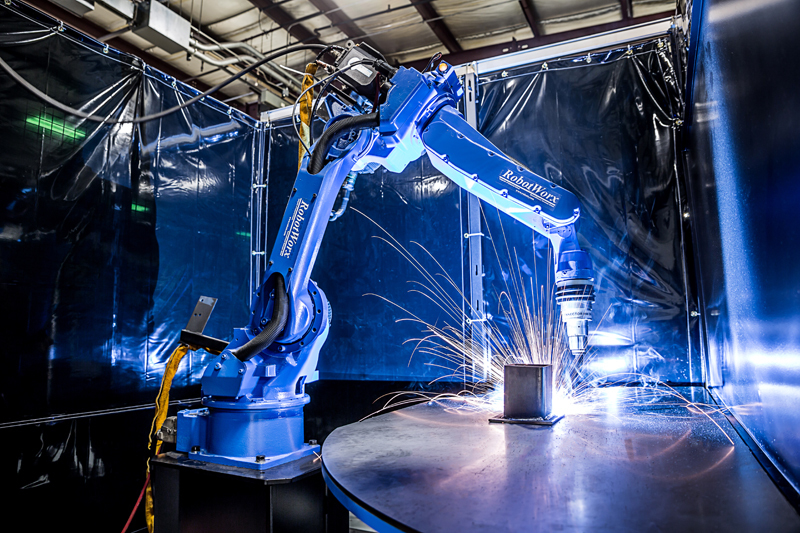
A robotic welder’s job is never done
As is common with most industries, the biggest factor to consider when making a capital purchase is “what kind of ROI will I see from my purchase?” When it comes to cost savings of robotic automation the roi is simple, one robot can work up to 24 hours a day with no downtime. That is something that would take three employees if they worked the average eight-hour shift. Not only do robots not require downtime, they are also far more efficient.
A robot welder uses select parameters to do their welding, this enables the robot to do more welding in less time than it takes the average person. Being able to deliver a better-quality product in less time will lead to better customer satisfaction which will in turn increase your repeat customer business. So now you are able to not only take on more customers AND keep them coming back.
But let’s talk real cost savings. The average robot is not an easy purchase, it is an investment. An investment that pays off in dividends at the end. But how do we find the real ROI?
We have the secret formula here at FanucWorld:
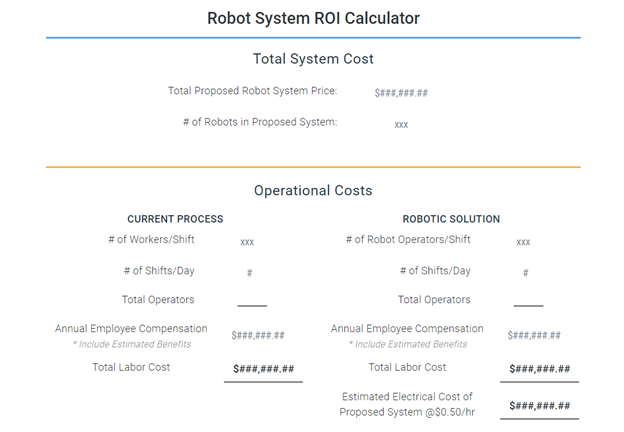
In the screenshot above you can calculate your own ROI by implementing your own businesses’ data into the labor fields on the left followed by your proposed robot solution on the right. If you need more information on robot welding solutions you can submit a quick quote request through our form located on our website. Our team of knowledgeable customer service representatives can help you find the right solution for your business and help you reach your full productivity potential in no time.
Get your Fanuc CNC machine back up and running.
TIE offers same day shipping on more than 100,000 Fanuc CNC parts in stock. We offer a 1 year in service warranty on all parts and repairs.
Shop PartsWas this helpful?
0 / 1