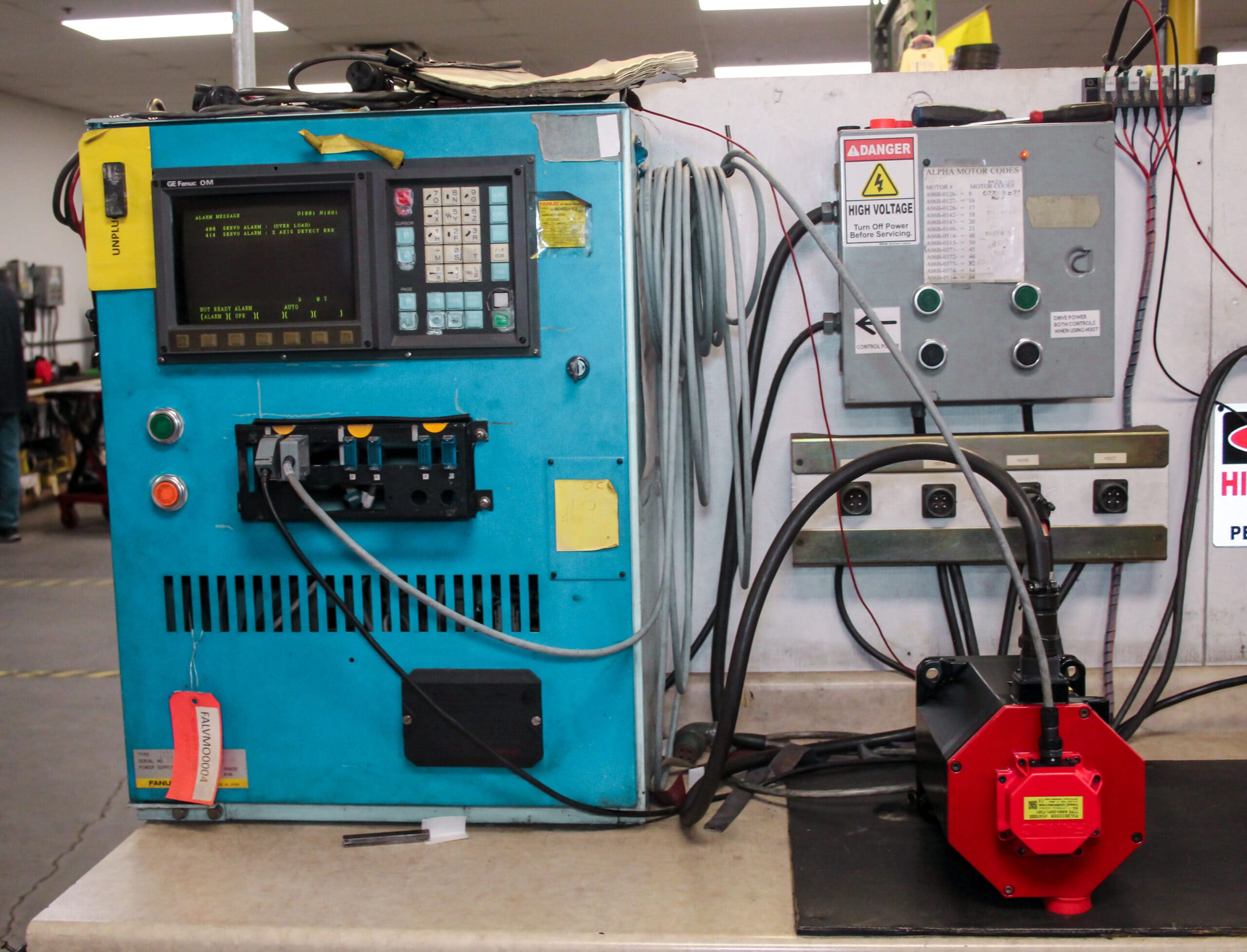
Even exceptional equipment like Fanuc robotics and CNC Machining Centers can sometimes encounter operational issues. While these robotic systems are known for reliability and precision, it is still to your advantage to be aware of common problems and solutions should they arise. This troubleshooting guide covers some of the most common problems users face with Fanuc robotic systems and CNC machines. Whether you’re dealing with motors moving in the wrong direction or various alarm codes, this FAQ will help you diagnose and resolve these issues efficiently before they interfere with your productivity and output.
Motor Moving in the Wrong Direction
Problem: Axis motor moving in the wrong direction.
Solution: A common misconception is that the motor is wired improperly. In a digital AC servo system, the CNC creates the waveform, and the motor’s encoder monitors its direction. The motor phase is reversed by changing a parameter setting, which dictates whether a positive move is clockwise or counterclockwise from the motor’s perspective. Another potential cause is a mistaken setting called mirror image, which reverses the programmed move direction.
High Current Alarms vs. Overcurrent Alarms
Problem: Receiving high current alarms (414 alarm) or overcurrent alarms.
Solution: These alarms differ in current monitoring specifics. A high current alarm, better described as an abnormal current alarm, is triggered by noise within the system. The servo drive monitors current quality and shuts down the machine if it detects noise. Causes can include defective servo drives or coolant contamination in the motor windings or cables. Inspect your cables carefully.
An overcurrent alarm indicates excessive current flow through the DC link, typically caused by system shorts. Common causes include unplanned contact, defective transistor modules, or dull tooling. To prevent these alarms, ensure all components are in good condition.
Soft Overtravel Alarm After Motor Replacement
Problem: Soft overtravel alarm occurs after motor replacement when attempting to reference.
Solution: This issue arises because the CNC machine remembers its last known position when it powers down. Upon restart, an incremental encoder requires repositioning. A soft overtravel alarm is triggered if the machine’s new position doesn’t match the last known position.
To resolve this:
- Power down the machine.
- Hold down the “P” key and the “Cancel” button.
- Power up the machine while continuing to hold these keys.
- The machine will ignore soft overtravels until the first zero reference position is set, clearing the alarm.
300 APC Alarm After Unplugging Motor
Problem: Receiving a 300 APC alarm after unplugging a motor.
Solution: A 300 APC alarm indicates the use of an Absolute Pulse Coder. Unlike Incremental Pulse Coders, which require machine referencing upon each startup, Absolute Pulse Coders have battery-backed memory to retain position information.
If this memory is lost due to an unplugged encoder cable, the machine will issue a 300-level alarm, signaling the need for re-referencing. Consult your machine tool builder manual for the proper referencing procedure.
Detailed Steps for Common Procedures
Changing Motor Direction
- Check Parameter Settings: Access the CNC’s parameter settings to verify the direction parameter.
- Adjust Direction Parameter: Modify the parameter to reflect the desired motor direction, clockwise or counterclockwise.
- Test Motor Movement: After adjusting the parameter, test the motor to ensure it moves in the correct direction.
Resolving High Current Alarms
- Inspect Cables: Inspect motor windings and cables for coolant contamination or damage.
- Check Servo Drive: Test the servo drive for defects and replace it if necessary.
- Monitor System Noise: Ensure the system is free from electrical noise that could trigger high current alarms.
Clearing Soft Overtravel Alarms
- Power Down the Machine: Ensure the machine is completely powered off.
- Hold “P” and “Cancel”: Press and hold these keys simultaneously.
- Power Up the Machine: Hold the keys as the machine powers up.
- Set Zero Reference Position: Once the machine is up, set the zero reference position to clear the alarm.
Addressing 300 APC Alarms
- Reconnect Encoder Cable: Ensure the encoder cable is securely connected.
- Replace Battery if Needed: If the battery for the Absolute Pulse Coder is depleted, replace it.
- Re-reference the Machine: Follow the machine tool builder’s manual to perform the correct referencing procedure.
Some issues can be resolved quickly, and others may require diagnostic research. By following the above steps and becoming knowledgeable about alarm codes, you can effectively troubleshoot and resolve common issues with Fanuc robotic systems and CNC machines.
For further assistance regarding Fanuc alarm codes or to purchase specific Fanuc parts, contact T.I.E. Industrial, a leading supplier of refurbished Fanuc replacement parts for CNC machines. Talk to our experts about resolving your Fanuc alarm code issues before equipment stoppages interfere with your company’s manufacturing operations.
Was this helpful?
0 / 0