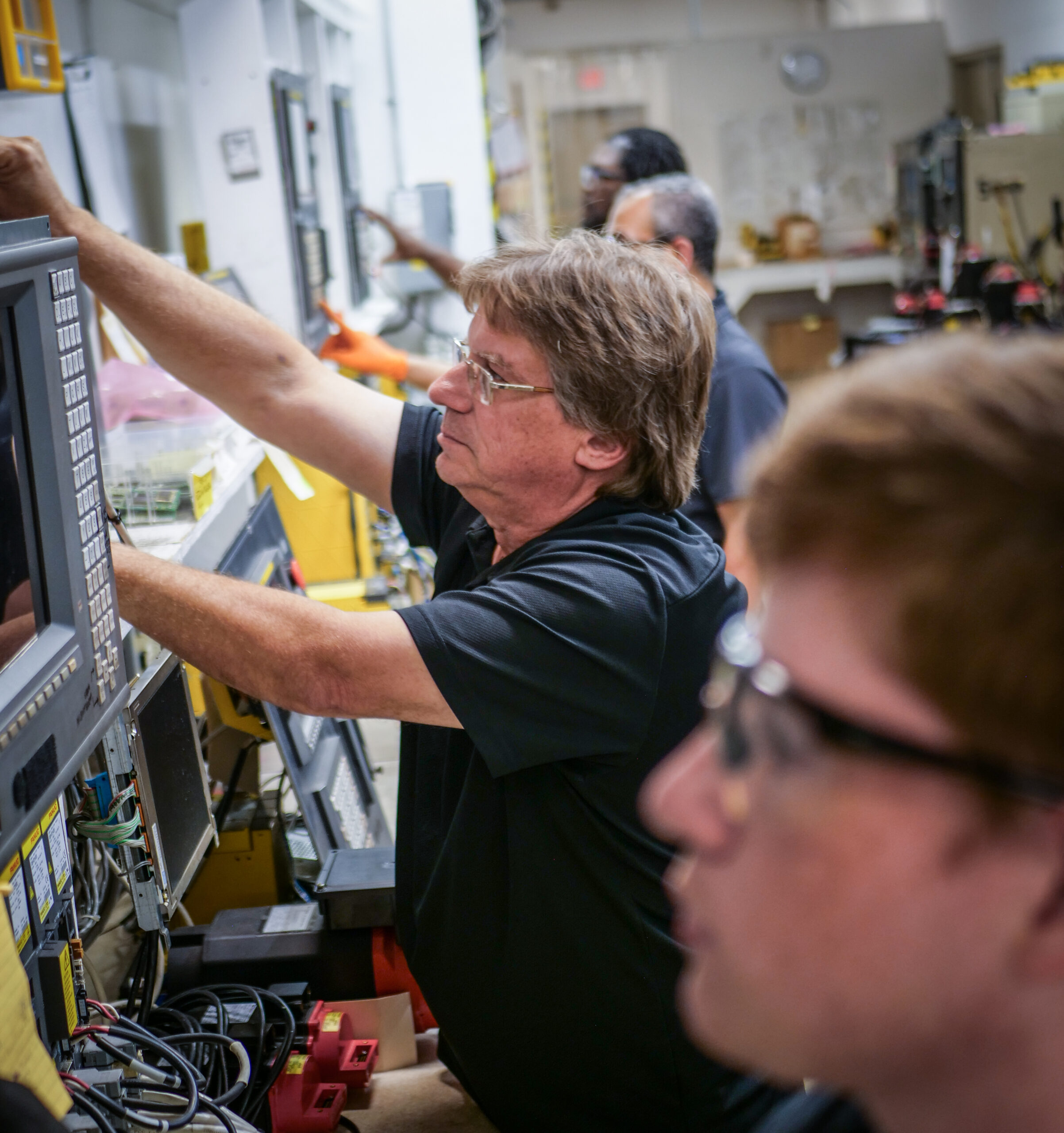
For manufacturing teams, CNC machines can seem challenging to operate at first, but with proper training, they become much easier to use.
As manufacturing continues to evolve, CNC training has become essential for modern manufacturing teams, ensuring operators and maintenance professionals have the necessary skills to keep production lines running smoothly. Companies risk inefficiencies, downtime, and costly errors without structured CNC training.
Let’s explore the challenges and the key benefits of CNC training, including how it improves efficiency, reduces downtime, and enhances troubleshooting. We will also outline the essential skills gained from a structured CNC training program.
CNC Machine Applications and Industries
CNC machines are used for numerous applications including lathing, milling, drilling, welding, grinding, and mold-making.
Industries that use CNC machines include automotive for engine and car parts, aerospacefor aircraft components, medical for prosthetics and surgical tools, electronics for circuit boards and electronic components, and metal fabrication for metal cutting and welding.
What Makes CNC Machines Challenging?
- Programming: CNC machines run on G-code, which requires learning a specific syntax. However, many modern CNC machines employ user-friendly interfaces or CAM software to simplify programming.
- Machine Setup: Operators must properly secure materials, set tool offsets, and calibrate the machine to ensure precision.
- Understanding Tooling: Different tools are used for cutting, drilling, and milling, and knowing which tool to use for each job is important.
- Troubleshooting: Issues like tool wear, misalignment, or incorrect programming can cause defects in the final product.
For beginners, CNC machines can be intimidating, but with training, they become a powerful and efficient tool for manufacturing.
The Importance of CNC Training in Manufacturing
CNC machines are integral to modern manufacturing, allowing companies to produce high-quality components with extreme precision. Proper training ensures that operators can handle CNC machines effectively, maximizing their capabilities.
1. Improving Efficiency with CNC Training
Efficiency is critical in any manufacturing environment. CNC machines streamline production processes by automating tasks and reducing manual labor. However, without proper CNC training, operators may struggle with programming, setup, and troubleshooting, leading to inefficiencies.
- Optimized Machine Operation: CNC training teaches operators how to properly set up and calibrate machines, reducing the risk of errors and rework.
- Faster Production Cycles: Skilled CNC operators can program machines to maximize speed and efficiency without compromising quality.
- Material Optimization: Training helps workers understand how to minimize material waste by using the correct cutting tools and techniques.
2. Reducing Downtime with CNC Training
Unplanned downtime can be costly, leading to lost productivity and increased operational expenses. CNC training equips maintenance teams with the skills needed to identify and address issues before they cause machine failures.
- Preventative Maintenance: Training programs cover routine maintenance procedures, helping workers keep machines in optimal condition.
- Rapid Troubleshooting: Skilled CNC professionals can quickly diagnose and fix errors, reducing the time spent on repairs.
- Minimized Errors: Proper training decreases the likelihood of programming mistakes that could lead to costly production halts.
3. Enhancing Troubleshooting and Robot Maintenance Skills
With the rise of automation, many CNC machines are integrated with robotic systems. As a result, CNC training also focuses on robot maintenance skills, ensuring that workers can handle CNC machines and the robots that support them.
- Robot Integration: Understanding how to program and maintain robots that assist CNC machines improves workflow automation.
- Diagnostics and Error Recovery: Trained professionals can analyze machine error codes and implement corrective actions.
- Adaptive Problem-Solving: CNC training fosters the ability to think critically and adapt to challenges in real time.
Key Skills Gained from CNC Training
A structured CNC training program provides essential skills that enhance performance and productivity.
- Blueprint Reading. Operators must be able to interpret technical drawings to program CNC machines correctly. Training helps workers understand dimensions, tolerances, material specifications, and geometric dimensioning and tolerancing (GD&T), ensuring precise machining.
- CNC Machine Operation. Workers learn to operate various CNC machines, including mills, lathes, and routers, gaining hands-on experience with different types of equipment. They also develop troubleshooting skills to handle common machine errors and maintain efficiency.
- G-Code and M-Code Programming. Programming is at the core of CNC machining. Training teaches operators how to write and edit G-code and M-code to control machine movements and functions. Advanced courses may also cover CAM software, which automates code generation for complex parts.
- Tool Selection and Setup. Choosing the right cutting tools and configuring them properly is critical for achieving high-quality results. CNC training covers tool types, speeds, feeds, and tool wear monitoring to optimize machining performance.
- Quality Control and Inspection. CNC training emphasizes quality assurance techniques, including part measurement, inspection tools, and adherence to industry standards. Operators learn to use calipers, micrometers, coordinate measuring machines (CMM), and other precision instruments to verify part accuracy.
By mastering these skills, CNC operators improve efficiency, reduce waste, and produce consistently high-quality components.
The Future of CNC Manufacturing and Smart Automation
Manufacturing is rapidly evolving, with new technologies such as smart manufacturing, additive manufacturing, and robotics playing a significant role. Companies investing in CNC training are better prepared to integrate these advancements into their operations.
- Additive Manufacturing: CNC is now combined with 3D printing to create complex components efficiently.
- Industrial Automation: Robots are increasingly used for CNC machine loading and unloading.
- Data Analytics in CNC: Smart manufacturing leverages real-time data to optimize machine performance and reduce waste.
Invest in CNC Training with T.I.E. Industrial
CNC training is essential for modern manufacturing teams, improving efficiency, reducing downtime, and enhancing troubleshooting capabilities. As CNC machines and robotics continue to evolve, skilled professionals are needed to operate and maintain them effectively.
T.I.E. Industrial provides refurbished CNC machines, replacement parts, and technical support to keep your manufacturing operations running smoothly. Whether you need high-quality CNC equipment, spare parts, or expert training, we have the solutions to meet your needs.
Explore our extensive inventory and expert services today. Visit T.I.E. Industrial to learn more about our CNC training and support.
Was this helpful?
0 / 0