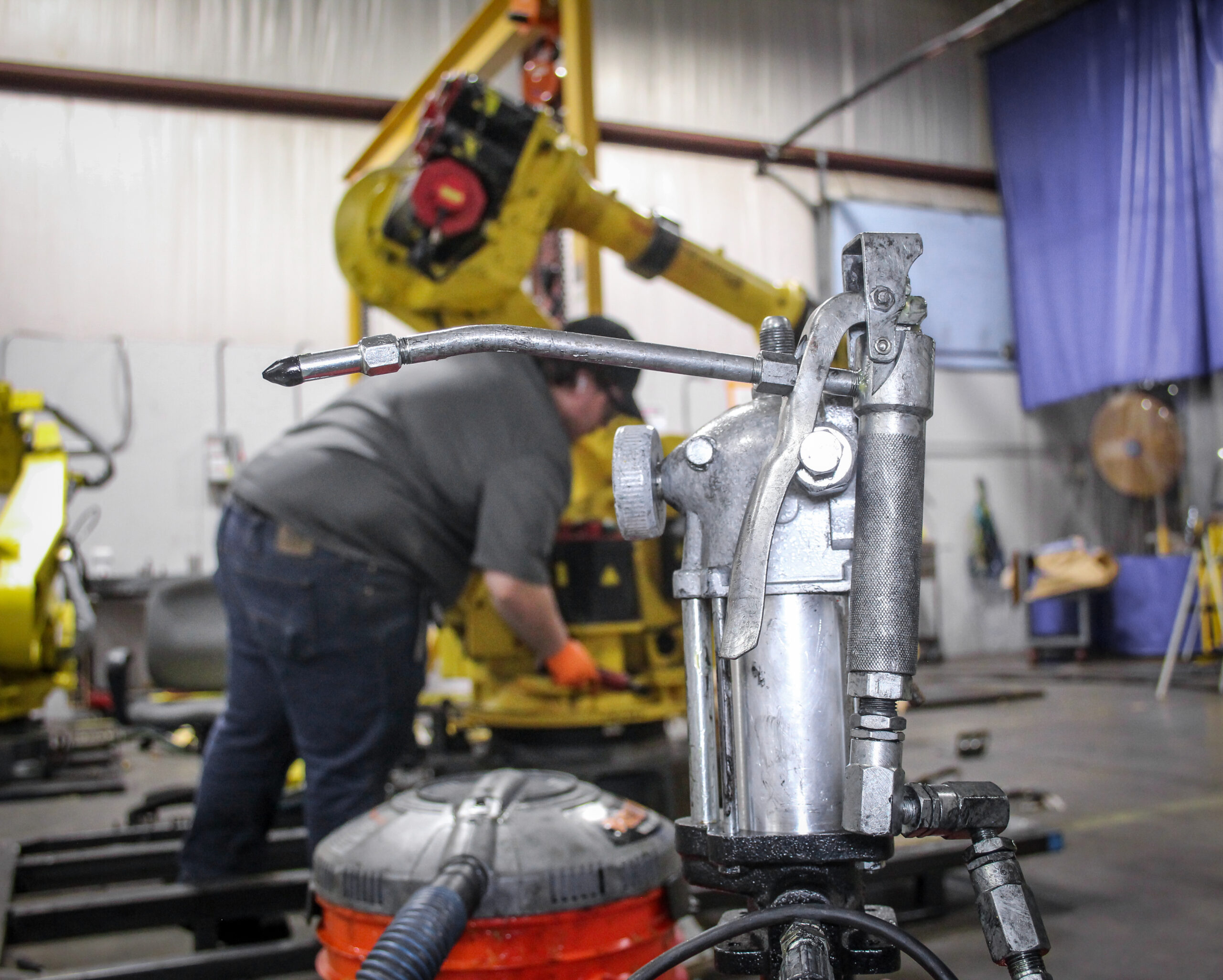
Industrial robots are built for precision and efficiency, but without proper lubrication to critical components like joints, bearings, and gearboxes, they can suffer fromincreased friction, overheating, and premature wear. Sometimes, industrial maintenance teams overlook greasing schedules or apply grease inconsistently, leading tounexpected breakdowns, costly repairs, and downtime.
Following manufacturer-recommended grease intervals and recognizing the signs that a robot needs lubrication are critical procedures. This guide will show how often different robot brands require greasing and how to spot lubrication issues, ensuring your robots operate efficiently and reliably.
The Purpose of Grease
Grease allows for smoother operations regarding robotic systems and parts by:
- Reducing friction, leading to smoother movement and better precision.
- Preventing overheating by dissipating excess heat generated during operations.
- Protecting gears, joints, and bearings from excessive wear.
Neglecting to grease your robot regularly can result in severe consequences, including components grinding against each other, leading to faster degradation, excessive friction resulting in mechanical failures, and expensive repairs.
How Often Should You Grease Your Robot?
The recommended grease interval varies by manufacturer, model, and workload. Below is a breakdown of manufacturer-recommended lubrication schedules:
- Standard models: Grease replacement every 3,850 hours.
- High-duty cycle robots: May require more frequent lubrication.
ABB Robots
- General lubrication cycle: Every 5,000 – 10,000 hours.
- Gear lubrication checks: Recommended every six months.
KUKA Robots
- Yearly grease replenishment required for planetary gear reduction units.
- Semi-annual inspections of grease levels help detect early wear or leaks.
Motoman Robots
- Grease replacement interval: Every 3,000 – 5,000 hours.
- High-speed models: May require more frequent lubrication.
Signs That Your Robot is Due for Lubrication
If a robot is overdue for lubrication, it will show performance issues. Warning signs include:
- Abnormal noises such as grinding or squeaking during movement.
- Resistance or sluggish motion in robotic joints.
- Overheating in gearboxes or motor areas.
- Visible grease contamination, including dried-out residue, leaks, or dirt buildup.
Ignoring these signs can lead to severe mechanical failures and increased downtime.
Step-by-Step Guide: How to Properly Grease an Industrial Robot
Proper lubrication is essential for maintaining the performance and longevity of industrial robots. Here’s a detailed guide to ensure effective greasing:
- Read the Manufacturer’s Manual. Provides essential information on the recommended grease, lubrication points, required quantities, and any special procedures or tools needed. Using the correct grease is crucial, as different models may require specific lubricants.
- Gather Necessary Tools and Materials. Assemble all required tools and materials before starting the greasing process. This includes:
- OEM-recommended grease
- Grease gun compatible with your robot’s grease fittings
- Clean rags or paper towels
- Protective gloves and safety glasses
- Containers or bags to collect expelled old grease
- Power On the Robot and Warm Up. Activate the robot and move it through its full range of motion to soften existing grease, making it easier to expel. Ensure all axes and joints are exercised to distribute heat evenly.
- Position the Robot for Maintenance. Place the robot in a stable position that allows easy access to all lubrication points.
- Identify and Clean Grease Ports. Locate the grease inlet and outlet ports on each axis or joint. Consult the manufacturer’s manual to identify them accurately. Clean the areas around these ports to prevent contamination during the greasing process.
- Remove Grease Plugs. Carefully remove the inlet and outlet grease plugs. This allows old grease to be expelled and provides an entry point for new grease. Ensure plugs remain free from contaminants during the process.
- Expel Old Grease. Operate the robot slowly to facilitate the expulsion of old grease to push out degraded lubricant, debris, and contaminants. Collect the expelled grease in a suitable container.
- Apply New Grease. Attach the grease gun to the inlet port securely. Slowly pump the recommended amount into the joint. Continue pumping until clean grease emerges from the outlet port, indicating that old grease has been fully displaced. Avoid over-greasing, as excessive lubricant can cause pressure buildup and potential seal damage.
- Reinstall Grease Plugs. Once new grease has been applied, stop the robot’s movement and reinstall the inlet and outlet plugs. Ensure they are secure to prevent leaks. Wipe away any excess grease from the exterior surfaces.
- Perform Post-Maintenance Testing. After reassembling, operate the robot through its full range of motion to distribute the new grease evenly across all components. Listen for unusual noises and observe the robot’s movements to confirm that the lubrication process has been successful and ensure that any air pockets are eliminated and the grease is seated correctly.
- Document the Maintenance Activity. Record the maintenance activity in the robot’s service log, noting the date, type of grease used, and any observations made during the process. This documentation is vital for tracking maintenance intervals and identifying potential issues.
Other Essential Robot Maintenance Tasks Beyond Greasing
While lubrication is vital, it is not the only maintenance task to keep industrial robots in peak condition. Other essential tasks include:
- Cleaning. Remove dust, debris, and excess grease to prevent contamination and improve performance.
- Calibration. Regularly check and adjust positional accuracy to ensure precision for automation tasks.
- Battery Maintenance. Inspect and replace backup batteries to prevent data loss and unexpected shutdowns.
- Component Replacement. Monitor motors, sensors, and gearboxes for wear and replace them before failure occurs.
Good Grease! Keep Your Robots Running Smoothly
A proper lubrication plan ensures that industrial robots remain reliable and productive for years. However, ensuring your robot operates at peak efficiency requires more than just lubrication—it demands high-quality components and expert support.
Trust T.I.E. Industrial, a leading supplier of high-quality refurbished robotic systems and replacement parts for your robot maintenance needs. With an extensive inventory of refurbished OEM and aftermarket components, expert technicians, and dedicated customer support, we help businesses maximize their robotic investments. Whether you need grease, gear replacements, or complete robotic systems, T.I.E. Industrial has the solutions to keep your robots running smoothly.
Contact us today to find the correct lubrication and maintenance solutions for your industrial robots.
Was this helpful?
0 / 0