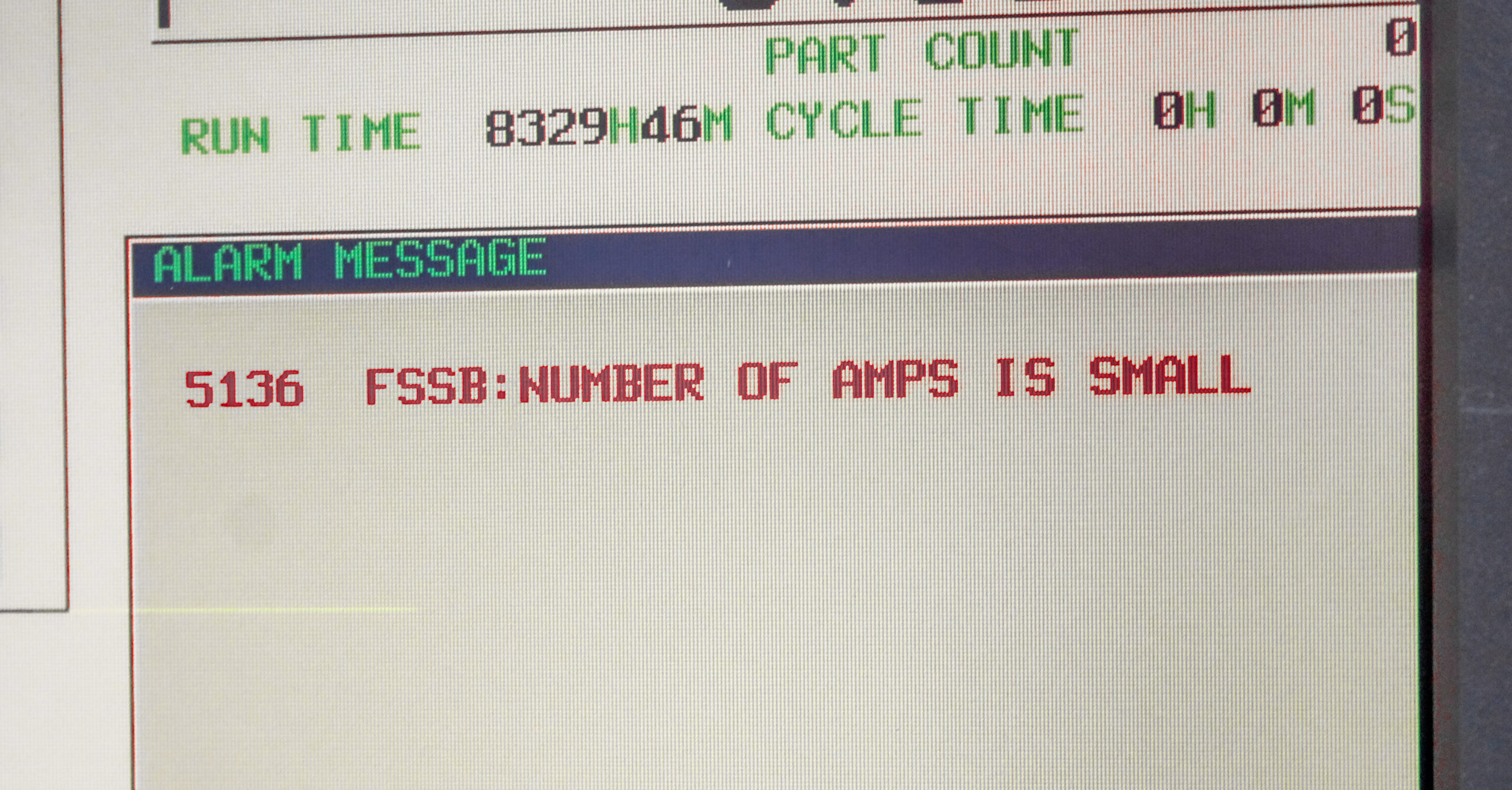
Of all the problems that occur on a factory floor, the words “operator error” regarding CNC machines can be avoided with proper training. CNC machines have revolutionized manufacturing by enabling precise and efficient production processes. However, even with advanced technology, operator errors can lead to significant issues such as increased scrap rates, extended cycle times, and costly machine crashes. Comprehensive CNC training is essential to mitigate these risks, ensuring optimal performance and safety in CNC manufacturing. Let’s look at some common errors and the solutions to prevent and address these issues.
Common CNC Operator Errors
- Inadequate Maintenance Practices
Neglecting regular maintenance tasks, such as cleaning and lubricating CNC machines, can result in debris accumulation. This buildup may cause overheating and adversely affect machining accuracy. For instance, failing to clean the machine properly can lead to spindle overheating, impacting the quality of the machined parts.
- Programming Errors
Errors in CNC programming, including incorrect code inputs or setup mistakes, directly impact the final product. Such mistakes can lead to dimensional inaccuracies or the creation of unintended features. For example, inputting incorrect variables into the program can cause the machine to execute unintended movements, resulting in defective parts.
- Incorrect Cutting Parameters
Using inappropriate feed rates and spindle speeds for specific materials and tools can result in poor surface finishes, tool breakage, or material deformation. For instance, setting a feed rate too high for a particular material can cause excessive tool wear and compromise the quality of the machined surface.
- Improper Tool Selection and Usage
Selecting unsuitable tools or using them incorrectly can damage both the tool and the workpiece, leading to undesirable surface finishes. For example, using a tool not designed for the material being machined can result in rapid tool wear and subpar product quality.
- Inaccurate Offset Settings
Failure to set tool and workpiece offsets accurately can lead to improper tool positioning relative to the workpiece, resulting in machining errors. This misalignment can cause dimensional inaccuracies and necessitate rework, increasing production time and costs.
- Material-Related Issues
Variations in material properties or failure to account for material deformation during machining can lead to inconsistencies in the final product. For instance, machining materials with varying hardness without adjusting parameters can result in uneven cuts and compromised product integrity.
The Impact of Operator Errors
Operator errors in CNC machining can have significant financial and operational consequences, affecting productivity, machine longevity, and overall manufacturing efficiency. Even minor mistakes can compound over time, leading to substantial losses.
- Increased Scrap Rates: Defective parts resulting from incorrect programming, tool misalignment, or material inconsistencies increase waste. Higher scrap rates drive up material costs and strain production schedules, forcing operators to manufacture replacement parts to meet demand.
- Extended Cycle Times: Errors often require operators to stop production, troubleshoot issues, and adjust, significantly prolonging cycle times. Reworking defective parts or recalibrating machines delays output, disrupting workflow and reducing the facility’s ability to meet deadlines.
- Machine Crashes: Severe programming or setup errors can result in tool collisions, spindle damage, or gantry misalignment, leading to costly repairs and machine downtime. Beyond the financial impact, crashes pose serious safety risks to operators, reinforcing the need for proper CNC training to prevent hazardous situations.
Comprehensive CNC training minimizes these risks, ensuring that operators understand best practices in programming, maintenance, and machine operation, leading to safer, more efficient, and cost-effective CNC manufacturing.
How CNC Training Prevents Operator Errors
Investing in comprehensive CNC training equips operators with the knowledge and skills to prevent common errors, enhancing efficiency and safety in CNC manufacturing.
- Emphasis on Regular Maintenance
Training programs highlight the importance of routine maintenance, teaching operators proper cleaning and lubrication techniques. This knowledge ensures machines operate optimally, reducing the risk of overheating and mechanical failures.
- Proficiency in Accurate Programming
Through training, operators learn to create precise CNC programs, minimizing the likelihood of errors that lead to defective parts. Understanding G-code and M-code instructions enables operators to input correct variables and set up machines accurately.
- Optimization of Cutting Parameters
Training provides insights into selecting appropriate feed rates and spindle speeds based on material properties and tooling requirements. This optimization enhances surface finish quality and extends tool life.
- Correct Tool Selection and Application
Operators learn to choose suitable tools for specific materials and applications, reducing the risk of tool damage and ensuring desired surface finishes.
- Accurate Offset Setting Techniques
Training emphasizes the importance of precise offset settings, enabling operators to position tools correctly relative to workpieces. This accuracy ensures dimensional integrity and reduces the need for rework.
- Understanding Material Properties
Comprehensive training includes education on material properties and behavior during machining. This knowledge allows operators to anticipate and compensate for material deformation, ensuring consistent product quality.
Benefits of In-Person CNC Training
While online resources offer valuable information, in-person CNC training provides hands-on experience and direct instructor interaction, leading to a deeper understanding of machine operations and maintenance.
- Hands-On Experience: In-person training allows operators to work directly with CNC machines, gaining practical skills immediately applicable in the workplace.
- Immediate Feedback: Direct interaction with experienced instructors enables immediate clarification of doubts and correction of techniques, fostering a more effective learning environment.
- Networking Opportunities: Participants can connect with peers and industry professionals, facilitating knowledge exchange and professional growth.
Invest in CNC Training and Rely on T.I.E. Industrial for Your CNC Needs
Operator errors can lead to costly downtime, scrap, and machine crashes, but proper CNC training can help avoid these mistakes. Investing in hands-on, in-person CNC training ensures operators develop the skills to maintain, program, and operate CNC machines effectively.
At T.I.E. Industrial, we understand the importance of precision, efficiency, and reliability in CNC manufacturing. That’s why we offer an extensive inventory of refurbished CNC systems, high-quality replacement parts, and technical support to keep your operations running smoothly. Whether you need robot maintenance skills, CNC training resources, or expert guidance, we have the solutions to support your business.
Don’t let CNC errors slow down your production. Visit T.I.E. Industrial today to explore our wide range of CNC machine error solutions, ensuring optimal performance and efficiency in your manufacturing facility.
Was this helpful?
0 / 0