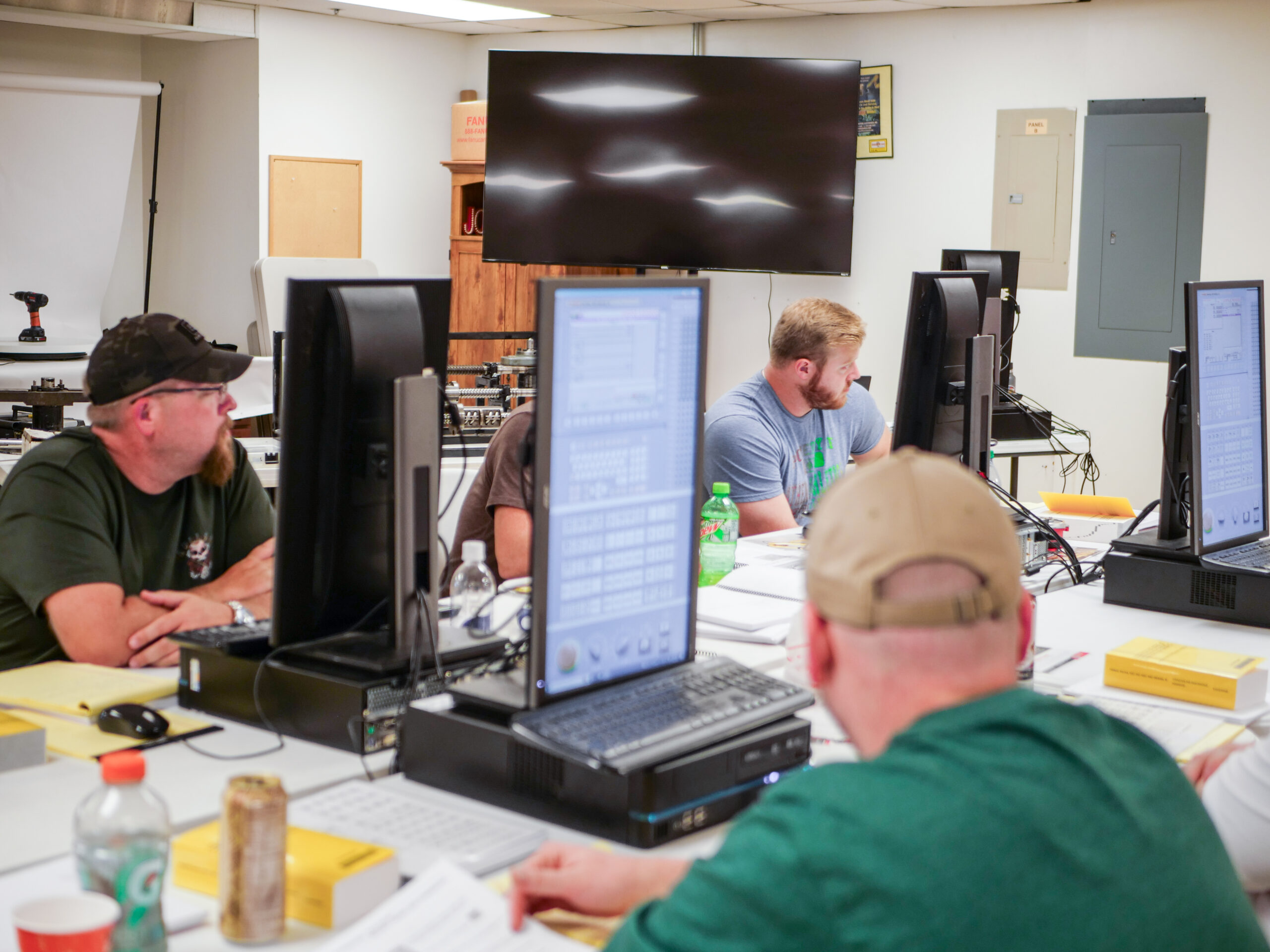
Entering the world of CNC manufacturing can be both exciting and overwhelming for new operators. CNC machines are powerful and complex tools that require a solid foundation of knowledge before operators can safely and efficiently work with them. Unlike manual machining, CNC technology relies on precise programming, automated tool movements, and strict operational procedures to ensure accuracy and consistency. New operators may struggle with setup, programming, troubleshooting, and machine maintenance without proper training, leading to costly mistakes and downtime.
A structured training program combining theoretical learning with hands-on practice is essential to get new CNC operators up to speed quickly. This approach not only builds confidence but also reinforces critical CNC skills such as G-code programming, workpiece setup, and machine safety. This guide will explore key learning areas for new operators and highlight the importance of foundational training before working on live machines.
Why CNC Training is Essential for New Operators
CNC training is crucial for entry-level operators to ensure safety, efficiency, and accuracy in manufacturing operations. Without proper training, new operators risk damaging machines, producing defective parts, or causing costly downtime. Investing in structured CNC training programs can:
- Reduce human error and material waste.
- Improve machine efficiency and productivity.
- Enhance safety and minimize workplace accidents.
- Ensure operators understand essential CNC maintenance skills.
- Build confidence and competence in machine operation.
For structured CNC training programs, explore Fanuc CNC Training.
Key Learning Areas for New CNC Operators
1. Foundational Knowledge
Before working on live machines, new CNC operators must first understand the basics of CNC machine operation, programming, and safety protocols. Core areas of focus include:
- CNC Machine Operation: Learning power-up/down procedures, emergency stops, machine controls, and basic settings.
- G-Code Fundamentals: Introduction to G-codes (G00, G01, G20, G21, etc.) and their role in controlling machine movements and operations.
- Machine Safety: Understanding personal protective equipment (PPE), machine guarding, and emergency shutdown procedures.
- Workpiece Setup: Learning proper workpiece clamping, alignment, and fixture techniques to ensure accurate machining.
- Tool Selection & Management: Identifying the correct tools for different materials and machining processes, along with maintenance practices.
- Spindle Speed & Feed Rates: Optimizing speeds and feeds based on material type and tooling to improve efficiency and part quality.
- Measuring Tools: Using calipers, micrometers, and other measuring tools to ensure machined parts meet tolerance specifications.
Explore more CNC learning resources at Fanuc In-Person Training.
2. Hands-On Practical Training
Learning CNC concepts in theory is not enough—new operators need hands-on experience to apply their skills. Effective practical training should include:
- Supervised Machine Operation: Allowing trainees to practice basic tasks such as setting up a machine, loading tools, and running simple programs under supervision.
- Simulators & Software: Utilizing CNC machine simulators to provide a safe environment for programming and troubleshooting before working on actual machines.
- Mentorship & Shadowing: Pairing new operators with experienced CNC professionals for guidance and real-world insights.
Hands-on training significantly enhances skill retention and prepares operators for real-world CNC manufacturing challenges.
3. Troubleshooting & Problem-Solving Skills
CNC operators will inevitably face issues such as tool breakage, program errors, or misaligned workpieces. Teaching them how to troubleshoot common problems can prevent costly mistakes and production delays. Key troubleshooting skills include:
- Identifying and resolving common CNC machine problems.
- Adjusting work offsets and tool wear compensation.
- Understanding alarm codes and machine diagnostics.
- Knowing when to seek assistance from maintenance personnel or senior operators.
4. Continuous Learning & Career Growth
CNC technology is constantly evolving, and staying up-to-date is essential for long-term career growth. Encouraging new operators to continue learning will improve their proficiency and open doors for career advancement. Recommended learning approaches include:
- Online Learning Resources: Utilizing CNC training websites, video tutorials, and industry forums.
- Formal Training Programs: Enrolling in structured courses offered by technical colleges or CNC training centers.
- Industry Certifications: Obtaining CNC machining certifications, such as those offered by Fanuc, to validate skills and enhance job prospects.
How Long Does It Take to Become a CNC Operator?
The time it takes to become a proficient CNC operator depends on the training method and hands-on experience. While some CNC training programs can be completed in a few weeks, it typically takes several months to a year for new operators to gain full proficiency. Factors that influence learning speed include:
- Prior experience in manufacturing or machining.
- Quality of training resources and hands-on practice.
- Complexity of the CNC machines and software being used.
- Availability of mentorship and real-world experience.
The Importance of In-Person CNC Training
While online CNC training resources are valuable, in-person training provides unparalleled benefits, including:
- Real-World Machine Operation: Training on actual CNC machines rather than relying solely on simulations.
- Immediate Instructor Feedback: Quick corrections and hands-on guidance from experienced professionals.
- Networking Opportunities: Connecting with other CNC professionals for career growth and industry insights.
- Greater Retention: Practical experience reinforces theoretical concepts and helps trainees retain skills more effectively.
Manufacturers looking for the best training solutions can explore Fanuc in-person training for high-quality CNC education.
Stay Ahead with CNC Training from T.I.E. Industrial
CNC training is an investment that pays off in increased efficiency, reduced errors, and improved workplace safety. New operators who undergo structured training programs gain the CNC maintenance skills and expertise needed to succeed in today’s fast-paced manufacturing industry.
At T.I.E. Industrial, we support CNC operators and manufacturers with:
- A vast inventory of refurbished CNC systems and replacement parts for leading brands.
- Technical support for CNC machines, robotic systems, and automation solutions.
- Training resources to help teams enhance their CNC skills and maintain peak efficiency.
Ready to start your CNC training journey? Explore our CNC training resources and equipment solutions at T.I.E. Industrial to take the next step toward becoming a skilled CNC operator!
Was this helpful?
0 / 0