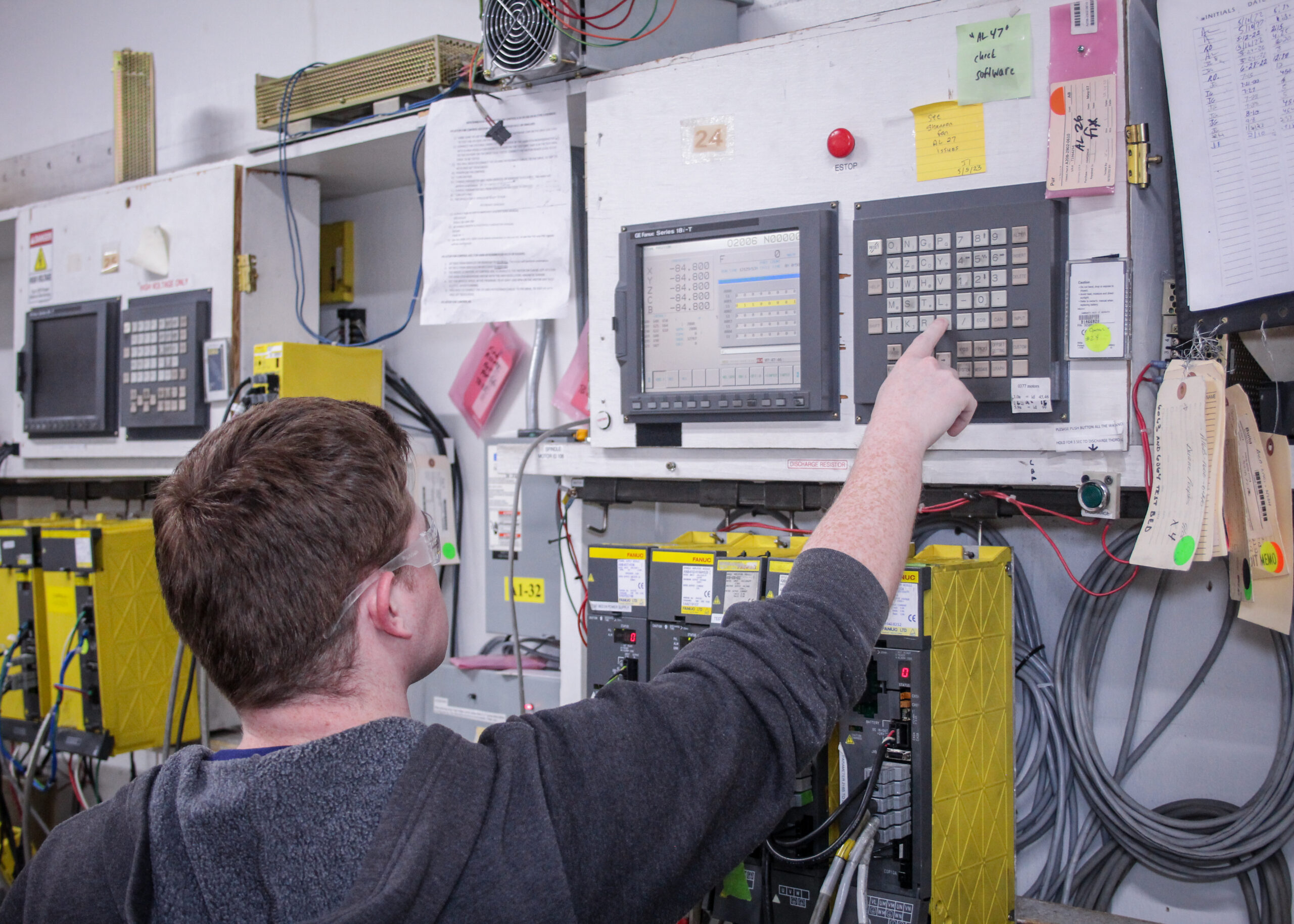
CNC machines used in numerous manufacturing sectors are synonymous with precision, efficiency, and productivity and rely on the expertise of CNC technicians. Without proper training, operators risk inefficiencies, costly errors, and extended downtime. Mastering key CNC skills ensures that technicians can effectively operate, troubleshoot, and maintain CNC machines, keeping production lines running smoothly.
This article highlights the top five CNC skills every technician should master, demonstrating how in-person training and hands-on experience play a crucial role in ensuring proficiency. By investing in CNC maintenance skills, manufacturers can increase uptime, reduce waste, and improve part quality.
CNC machines used in numerous manufacturing sectors are synonymous with precision, efficiency, and productivity and rely on the expertise of CNC technicians. Without proper training, operators risk inefficiencies, costly errors, and extended downtime. Mastering key CNC skills ensures that technicians can effectively operate, troubleshoot, and maintain CNC machines, keeping production lines running smoothly.
This article highlights the top five CNC skills every technician should master, demonstrating how in-person training and hands-on experience play a crucial role in ensuring proficiency. By investing in CNC maintenance skills, manufacturers can increase uptime, reduce waste, and improve part quality.
1. CNC Programming: The Backbone of Precision Manufacturing
Why It Matters
CNC programming is the foundation of machining operations, enabling automated precision in manufacturing. Skilled programmers can optimize G-code and M-code, reducing cycle times, improving accuracy, and extending tool life.
Key Learning Areas
• G-code and M-code mastery: Writing, troubleshooting, and optimizing machine code for precision, efficiency, and complex machining tasks.
• CAD/CAM software proficiency: Using programs like Autodesk Fusion 360, Mastercam, and SolidWorks to create and simulate toolpaths.
• Parameter optimization: Adjusting spindle speeds, feeds, depth of cut, and tool engagement for different materials, cutting tools, and machining strategies.
Real-World Example: Aerospace Industry
In aerospace, precision is non-negotiable. A leading supplier trained its CNC operators in advanced programming techniques, reducing material waste by 15% and improving machining accuracy, ensuring compliance with strict aerospace standards.
2. Machine Setup and Calibration: Ensuring Accuracy from the Start
Why It Matters
Proper machine setup reduces errors, enhances repeatability, prevents costly rework, and improves overall machining efficiency. A well-prepared setup ensures that tools, workpieces, and fixtures are accurately positioned, minimizing scrap and maximizing productivity.
Key Learning Areas
• Workpiece alignment and fixturing: Ensuring secure, precise placement of materials to prevent movement, vibration, or misalignment during machining operations.
• Tool offsets and calibration: Setting correct tool lengths, work offsets, and verifying spindle alignment for consistent accuracy across multiple parts.
• Material selection and handling: Choosing the right material based on machinability, thermal expansion, and strength while ensuring proper storage and handling to prevent contamination or warping.
Real-World Example: Medical Device Manufacturing
A medical device manufacturer reduced setup time by 25% by training operators in advanced fixturing techniques. This led to increased throughput without sacrificing precision, meeting strict FDA quality standards.
3. Troubleshooting and Problem-Solving: Minimizing Downtime
Why It Matters
A trained technician with strong troubleshooting skills can quickly diagnose and resolve issues, preventing excessive downtime, lost revenue, and potential damage to machine components. Understanding how to interpret machine diagnostics, alarms, and mechanical failures is crucial for maintaining smooth operations and extending equipment lifespan.
Key Learning Areas
• Identifying common errors: Understanding error codes, machine alarms, and system diagnostics to pinpoint electrical, software, or mechanical issues.
• Diagnosing tooling failures: Recognizing wear patterns, breakage causes, and optimizing tool life through proper feeds, speeds, and coolant application.
• Resolving spindle and drive issues: Addressing vibration, overheating, misalignment, and axis drive faults to maintain precision and performance in machining operations.
Real-World Example: Automotive Industry
A leading automotive manufacturer implemented a troubleshooting certification program, resulting in a 30% reduction in machine stoppages. Operators became adept at diagnosing and fixing tool breakage issues, keeping production lines moving efficiently.
4. Preventative Maintenance: Extending Machine Lifespan
Why It Matters
Preventative maintenance is essential for avoiding unexpected failures and costly repairs. A well-maintained CNC machine operates at peak efficiency, reducing scrap, downtime, and the risk of catastrophic breakdowns. Regular maintenance extends the lifespan of critical components, ensures consistent precision, and minimizes production disruptions. Skilled technicians can identify wear patterns and implement proactive measures to keep machines running smoothly.
Key Learning Areas
• Lubrication and cleaning protocols: Keeping machines in top condition by applying proper lubricants, removing debris, and preventing contamination that can affect performance.
• Monitoring spindle health: Using vibration analysis, thermal monitoring, and load detection to identify early signs of wear or imbalance before failure occurs.
• Replacing worn components: Identifying when to replace ball screws, bearings, belts, and way covers to maintain accuracy, rigidity, and smooth machine movement.
Real-World Example: Heavy Equipment Manufacturing
A construction equipment manufacturer reduced unscheduled downtime by 40% after implementing a preventative maintenance program. CNC technicians were trained in predictive maintenance techniques, ensuring continuous operation.
5. Advanced Machining Techniques: Boosting Productivity and Quality
Why It Matters
Technicians must stay ahead by learning advanced machining techniques that improve efficiency, part quality, and overall manufacturing competitiveness. Mastering these skills allows machinists to optimize production, reduce waste, and take advantage of cutting-edge technology.
Key Learning Areas
• High-speed machining: Reducing cycle times while maintaining accuracy, improving surface finishes, and minimizing tool wear through optimized feed rates and spindle speeds.
• Multi-axis machining: Enhancing complex part production with simultaneous movement across multiple axes, enabling intricate geometries and reducing the need for multiple setups.
• Automation integration: Understanding how CNC machines work alongside robotic systems, pallet changers, and automated tool changers to increase productivity and reduce manual labor.
Real-World Example: Precision Tooling Industry
A precision tooling company adopted multi-axis machining training, enabling operators to produce complex geometries 35% faster while maintaining high precision. This resulted in a significant competitive advantage in custom tooling production.
Why CNC Training is Essential for Success
Continuous learning ensures that CNC technicians stay up-to-date with industry advancements and best practices. In-person training and structured certification programs provide hands-on experience, ensuring that technicians can apply their skills effectively.
Benefits of Ongoing CNC Training
✅ Reduces downtime by improving problem-solving skills.
✅ Increases productivity through optimized machining processes.
✅ Enhances part quality with precise programming and setup.
✅ Extends machine lifespan with preventative maintenance techniques.
✅ Boosts career opportunities by providing in-demand CNC skills.
Master CNC Skills with T.I.E. Industrial
Mastering these top five CNC skills is critical for technicians who want to excel in CNC manufacturing. Skilled operators are the backbone of efficient production, and investing in CNC training leads to higher efficiency, lower costs, and improved machine longevity.
T.I.E. Industrial is a trusted provider of refurbished CNC systems, replacement parts, and technical support. Whether you need CNC maintenance skills, in-person training, or high-quality CNC equipment, we have the solutions to keep your operations running smoothly.
Explore our extensive inventory of CNC parts and training programs. Contact T.I.E. Industrial today to enhance your CNC workforce.
Was this helpful?
0 / 0