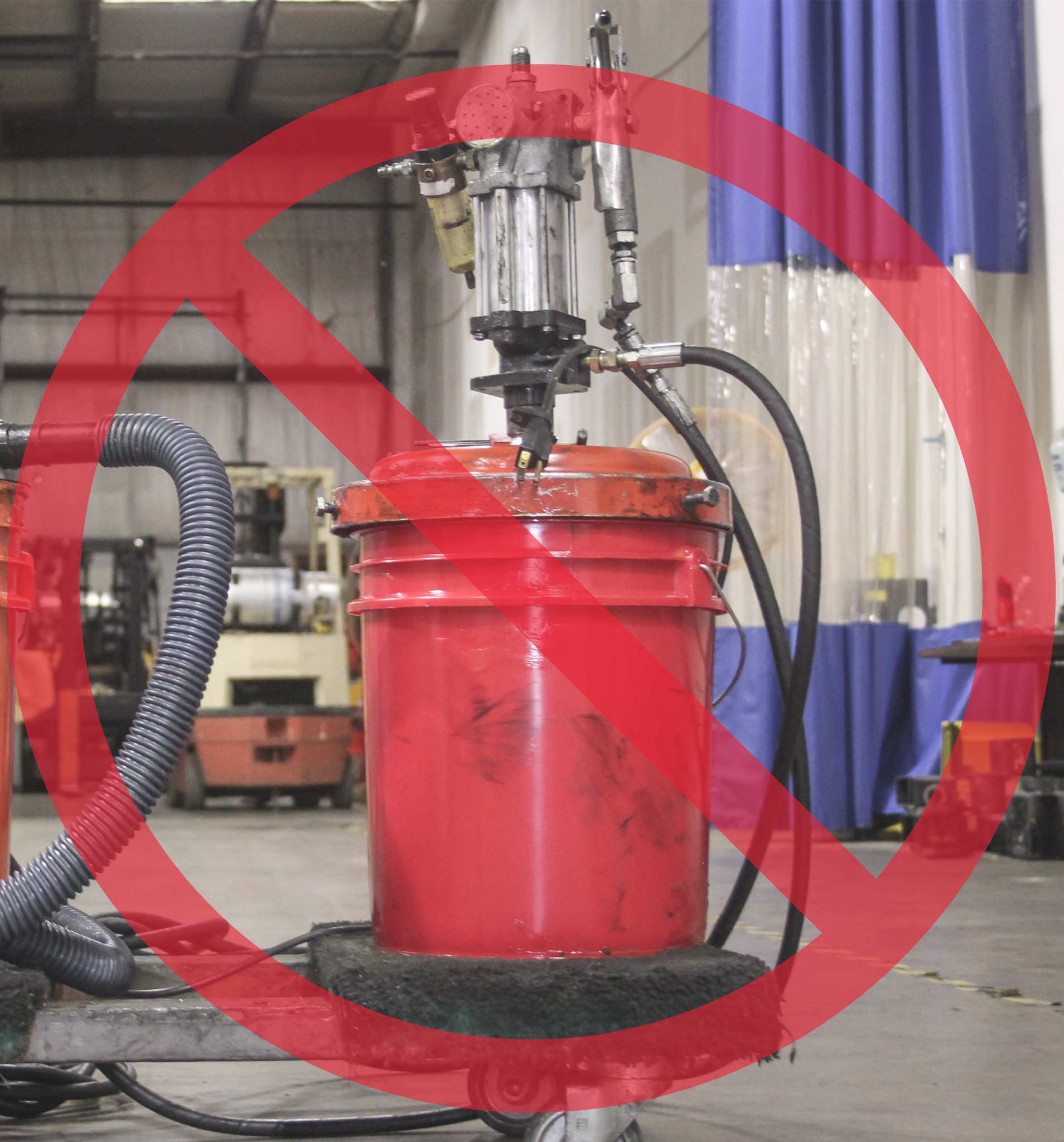
Numerous industries will quickly agree that robots are indispensable assets, performing tasks with precision and efficiency. Regular maintenance—particularly proper lubrication—is crucial to maintaining their optimal performance. Using the correct grease ensures smooth operation, reduces wear, and extends the lifespan of robotic components. Conversely, incorrect or substandard grease can lead to significant issues, affecting productivity and profitability.
The Importance of Correct Grease Selection
Selecting the appropriate lubricant for industrial robots is not merely a recommendation but a necessity. The right grease minimizes friction between moving parts, prevents overheating, and protects gears and joints from premature wear. Conversely, using the wrong lubricant can increase friction, overheating, and accelerated wear. This misstep can result in unexpected breakdowns and costly repairs.
The Price of the Wrong Grease: Costly Mistakes Your Business Can’t Afford
Using incorrect grease in industrial robots can lead to significant operational challenges, impacting efficiency and profitability. Key consequences include:
- Increased Wear and Tear
The primary function of grease is to minimize friction between moving parts. An inappropriate lubricant can result in inadequate lubrication, leading to metal-to-metal contact. This accelerates the deterioration of components such as bearings and gears.
- Overheating
Proper lubrication facilitates effective heat dissipation within robotic components. Incompatible lubricants may fail to dissipate heat efficiently, causing components to overheat. This overheating can lead to system failures and reduced operational lifespan. Additionally, certain applications can result in higher current consumption and increased energy usage due to inadequate lubrication at startup.
- Contamination
Using the wrong grease can lead to chemical reactions that produce harmful byproducts, contaminating the lubrication system and damaging components. This contamination can increase friction, wear, and potential system failures. For example, using a lubricant with incompatible additives can cause chemical reactions that degrade the lubricant and harm the components.
- Costly Downtime
Mechanical failures due to improper lubrication can lead to unexpected downtime, affecting production schedules and incurring significant repair costs. For instance, excessive lubrication can lead to clogged lubrication points, sealing failures, and deterioration of parts, resulting in production stoppages for repairs and maintenance.
Manufacturer-Specific Grease Recommendations
Each robot manufacturer specifies particular grease types and lubrication intervals tailored to their models. Adhering to these guidelines is vital for maintaining robot health and performance.
- Fanuc Robotsrecommends using VIGOGREASE REO for their robots. This grease addresses challenges associated with previous lubricants, offering superior performance and reducing issues like oil separation and leakage. MolyWhite grease has been standard for older models, but transitioning to VIGOGREASE REO is advisable for enhanced reliability.
- KUKA Robots specifies the use of their proprietary gear oil for their robots. For instance, the KUKA KR QUANTEC series requires using KUKA GearOil 460 for its gear units.
- MOTOMAN Robots require specific lubricants for their gear systems. For example, the MOTOMAN MH24 model uses Yaskawa’s MP-2 grease for its gear units. Using the correct grease ensures the longevity and reliability of the robot’s mechanical components.
- ABB Robots recommends the use of their proprietary lubrication products for their robots. For instance, the ABB IRB 6700 series requires using ABB’s Lubrication Grease 23 for its gear units.
And Ounce of Prevention: Preventative Measures Using the Correct Grease
Proper lubrication is essential for the optimal performance and longevity of industrial robots. To mitigate the risks associated with improper lubrication, consider the following strategies:
- Adhere to Manufacturer Guidelines
Manufacturers provide specific lubricant recommendations and maintenance intervals tailored to each robot model. Following these guidelines ensures that the lubricants are compatible with the robot’s materials and operating conditions, preventing premature wear and mechanical failures. For instance, using the correct lubricant can regulate temperatures and loads, maintaining the robot’s precision over time.
- Regular Inspections
Incorporating routine lubrication checks into maintenance schedules is vital for early detection of potential issues. Over time, grease can break down due to friction and heat, reducing its effectiveness. Regular inspections help identify signs of lubricant degradation, contamination, or insufficient application, allowing for timely corrective actions. This proactive approach minimizes the risk of unexpected downtime and extends the service life of robotic components.
- Training and Certification
Ensuring that maintenance personnel are trained and certified in proper lubrication techniques specific to each robot model is crucial. Proper training equips technicians with the knowledge to select appropriate lubricants, apply them correctly, and recognize early signs of lubrication-related issues.
- Consult Experts
Consulting with professionals or the robot manufacturer is advisable. Experts can provide insights into selecting the most suitable lubricants, adjusting maintenance schedules based on operating conditions, and implementing best practices.
Organizations can significantly reduce the risks associated with improper lubrication by adhering to manufacturer guidelines, conducting regular inspections, investing in training and certification, and consulting experts. These proactive measures ensure that industrial robots operate efficiently, safely, and with minimal downtime, ultimately contributing to increased productivity and cost savings.
Lubrication Lessons Learned: Ensure Robots Peak Performance
Proper lubrication is the lifeblood of industrial robots, ensuring their reliability and efficiency. Using the correct grease as specified by manufacturers like Fanuc, KUKA, MOTOMAN, and ABB is paramount in preventing premature wear, overheating, and costly downtime.
At T.I.E. Industrial, we understand the critical importance of proper maintenance in extending the lifespan and performance of your robotic systems. As a leading supplier of high-quality refurbished robots, robotic systems, and replacement parts, we offer:
- Extensive Inventory: A wide range of refurbished robots and replacement parts from leading brands ensure you find the necessary components.
- Expert Technicians: Our team of certified professionals provides unparalleled support, ensuring your robots operate at peak performance.
- Exceptional Customer Support: We are committed to delivering outstanding service and assisting you at every step to maintain and enhance your robotic systems.
Partner with T.I.E. Industrial to ensure your robots receive the best care, maximizing productivity and minimizing downtime. Contact us today to learn more about our products and services.
Was this helpful?
0 / 0