Keeping industrial robots in top shape takes more than just uptime—it depends on grease, timing, and how you manage both. Whether you’re overseeing a high-throughput cell or running a tight CNC shop, lubrication methods directly impact performance, lifespan, and cleanup. You’ve probably seen both ends of the spectrum: the technician with a grease gun and a printout, and the automated setup quietly handling it in the background.
This article breaks down the basics of manual vs. auto-lubricating system options, so you can decide what fits your operation best. Expect straight comparisons, real trade-offs, and the kind of details that matter when you’re the one responsible for keeping robots moving.
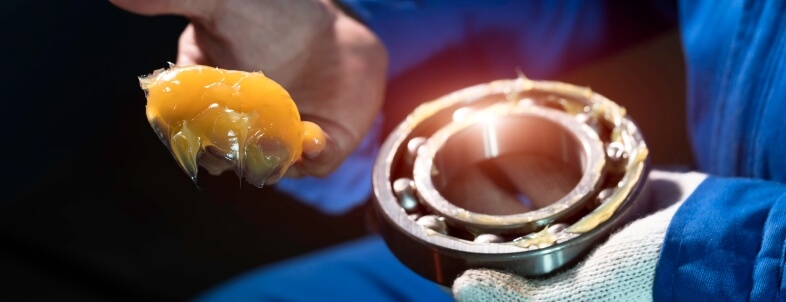
- Why Lubrication Methods Matter
- Manual Greasing Systems
- Automated Greasing Systems
- Comparing Lubrication Methods
- Choosing the Right System
- What To Consider
- Frequently Asked Questions
Why Lubrication Methods Matter
Every moving part in an industrial robot is under constant stress, especially in high-cycle or high-load environments. Without the right lubrication methods, even the best-built machines wear down faster than they should. Grease is a critical part of keeping joints, bearings, and gears from grinding themselves into early failure.
Missed intervals, inconsistent application, or using the wrong grease altogether can lead to overheating, backlash, or full mechanical breakdowns. That’s why the method you use to apply grease matters. Whether it’s a technician doing scheduled work with a manual pump or a fully automated robot grease application system tied to runtime counters, your approach affects everything from downtime to part life.
If you’re working with legacy systems or a mix of new and old robots, choosing the right system means keeping machines running cleanly, smoothly, and predictably.
Manual Greasing Systems for Robots
Manual greasing systems for robots are exactly what they sound like—technicians apply lubricant by hand, usually following a set schedule based on hours of operation or calendar intervals. This process often involves:
- Accessing grease fittings with a manual pump
- Wiping away old residue
- Verifying application points by sight or feel
Advantages
The upside is simplicity. These systems require minimal hardware investment and give maintenance teams direct control over what gets greased and when. They’re especially common in smaller facilities or with older robot models that don’t support automated options.
Disadvantages
But there are drawbacks. Manual systems depend on technician consistency. Missed applications, over-greasing, or under-greasing can lead to wear, contamination, or unplanned downtime. On busy floors, it’s easy for scheduled maintenance to fall behind, which only makes the risk higher.
Manual greasing systems for robots can work well, but they rely heavily on time, training, and tight maintenance discipline.
Automated Greasing Systems for Robots
Automated greasing systems for robots take the manual labor out of lubrication, applying grease at the right times and in the right amounts without needing a technician to step in. These systems often sync with the robot’s control setup, using timers or sensors to track usage and determine when it’s time to grease.
Advantages
The key benefit here is consistency. An automatic greasing system ensures that every part of the robot gets the proper lubrication, exactly when needed. This eliminates the risk of human error, like missing a scheduled application or over-greasing, which can cause wear or downtime. It also helps keep robots running smoothly, reducing the need for frequent repairs or interruptions.
Another big advantage is cleaner operation. With automated robot grease application, there’s less chance for contamination, since the system applies grease in a controlled, measured way.
Disadvantages
Of course, these systems come with a higher upfront cost, particularly if you’re retrofitting older robots. They can also require more attention when it comes to maintenance or troubleshooting.
But for operations with high-volume or complex robotic setups, automated greasing systems for robots can save both time and money in the long run, reducing manual maintenance efforts and preventing costly breakdowns.
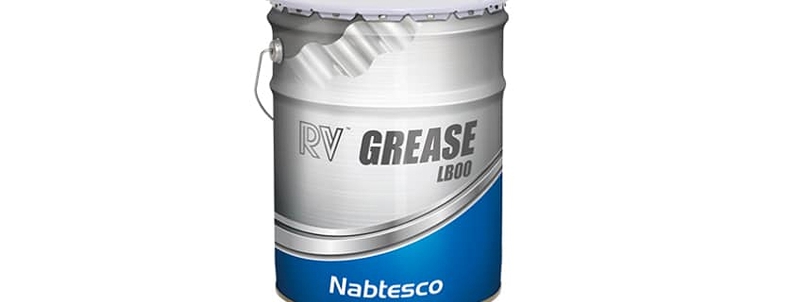
Order Robot Lubricants from T.I.E. Industrial
Need the right grease to keep your robot parts moving? Order directly from T.I.E. Industrial and get OEM-approved lubricants shipped fast.
Compatible with numerous modelsStocked and ready to ship—no long lead timesBacked by expert support if you’re not sure what you need
Comparing Lubrication Methods Side-by-Side
When you’re choosing between manual and automated greasing systems for robots, understanding the key differences can help you make an informed decision. Here’s a straightforward comparison to guide you:
Feature | Manual Greasing Systems | Automated Greasing Systems |
---|---|---|
Cost | Lower upfront cost, but more time and labor involved | Higher initial cost, but less ongoing maintenance |
Consistency | Depends on technician’s timing and attention | Consistent, precise lubrication every time |
Labor | Requires regular human intervention | Minimal labor once installed |
Risk of Error | Higher chance of human error (missed or incorrect application) | Reduced risk of mistakes, but dependent on system setup |
Maintenance | Simple maintenance but needs scheduling and discipline | Low maintenance, but may need occasional troubleshooting |
Speed | Slower—each application takes time and focus | Faster, can apply lubrication during robot downtime |
In terms of performance, automatic greasing systems often shine in high-demand environments where uptime and consistency are critical. The system can grease while the robot runs, ensuring lubrication doesn’t interrupt production.
However, manual greasing systems for robots have their place, particularly in smaller or older setups. They’re ideal for environments where the robot isn’t running nonstop or where a more hands-on approach is needed.
Choosing the Right System for Your Operation
If you’re considering a manual vs auto-lubricating system, there’s no universal right answer. It depends on your setup, your team, and how you use robots day to day.
High-volume shops with nonstop operations often lean toward automated greasing systems for robots because they reduce interruptions and keep maintenance consistent without extra labor. On the other hand, smaller facilities or those with legacy machines may stick with manual greasing systems, especially if budgets are tight or the robots aren’t in constant motion.
Your decision should factor in how often robots run, how many you’re maintaining, and whether your team can realistically keep up with manual lubrication schedules. Some shops go hybrid, using automated robot grease application for high-demand units and sticking with manual methods for less critical ones.
Either way, the goal is the same: clean, consistent grease application that keeps failures off the schedule and production on track.
Trust T.I.E. Industrial for the Robot Grease and Lubricants You Need
What To Consider Moving Forward
Whether you’re running one robot or an entire line, lubrication demands attention, unless you’ve automated it to handle the job without fail. Choosing the right manual vs. auto-lubricating system setup comes down to how your operation works, how much downtime you can afford, and how tight your maintenance schedule is.
If you’re ready to make a move, T.I.E. Industrial has you covered. From OEM-grade grease to expert advice, we have what you need to keep things running clean.
Frequently Asked Questions About Manual vs. Auto-Lubricating Systems
Still weighing your options? These quick answers clear up common questions about lubrication methods and what makes sense for your setup.
Can automated systems replace all manual greasing tasks?
Not always. While automated greasing systems for robots can handle most routine lubrication, some hard-to-reach fittings or older components may still require occasional manual attention.
Is there a difference in the type of grease used for manual vs. auto-lubricating systems?
Sometimes. Most of the time, the grease itself is the same, but automated systems may require specific viscosity or cartridge-compatible formulations to flow properly and avoid clogging.
How long does it take to see ROI on an automated greasing system?
That depends on usage, downtime costs, and maintenance staffing. High-use operations often see a return on investment within 12 to 18 months, especially when reduced wear and fewer shutdowns are factored in.
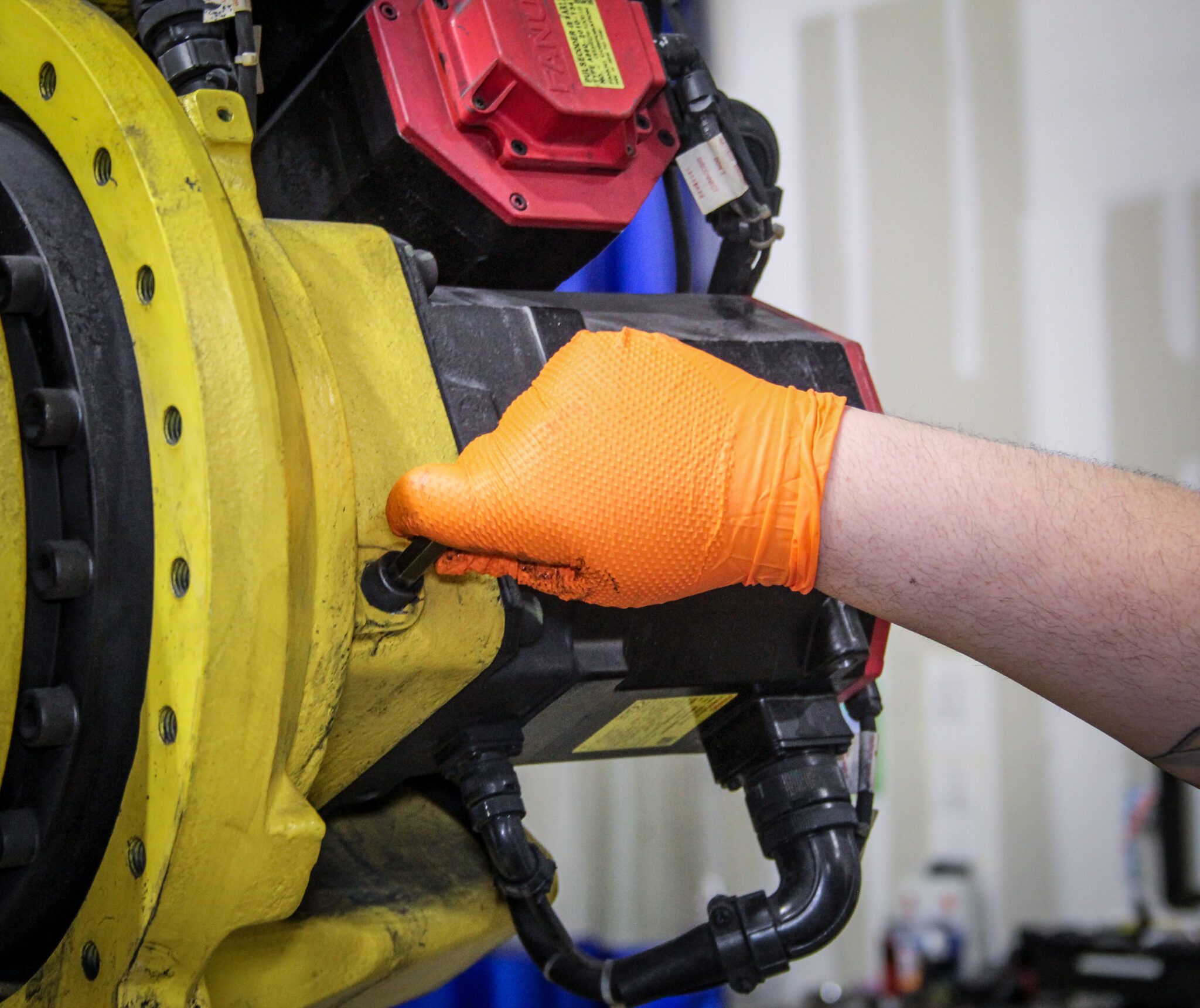
A Step-by-Step Guide to Greasing Your Robot’s Joints and Gears
Get in-depth information on the best way to lubricate your robots gears and joints.
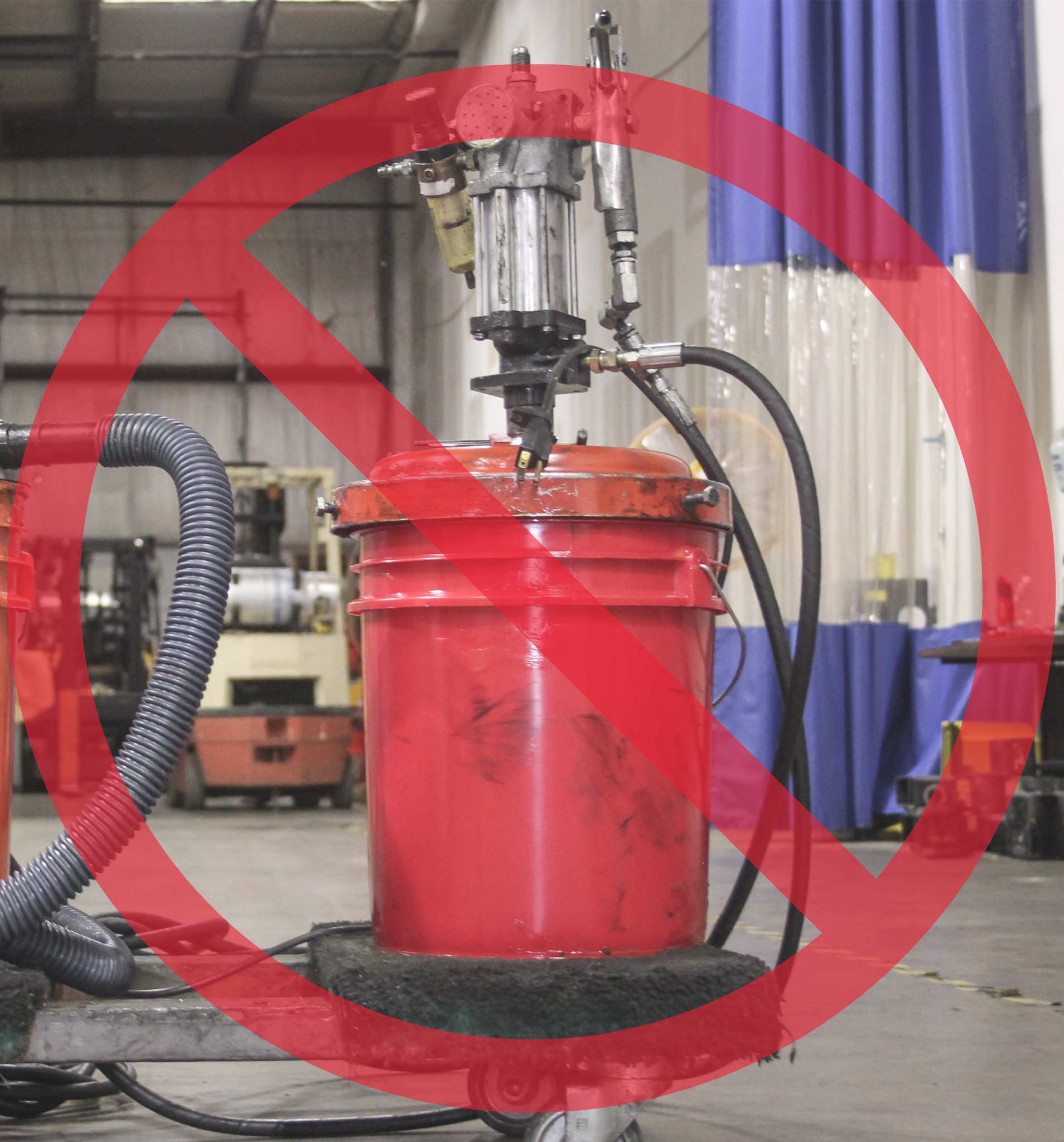
The Consequences of Using the Wrong Robot Grease
Discover everything that can go wrong if you don’t use the correct grease for your robots.
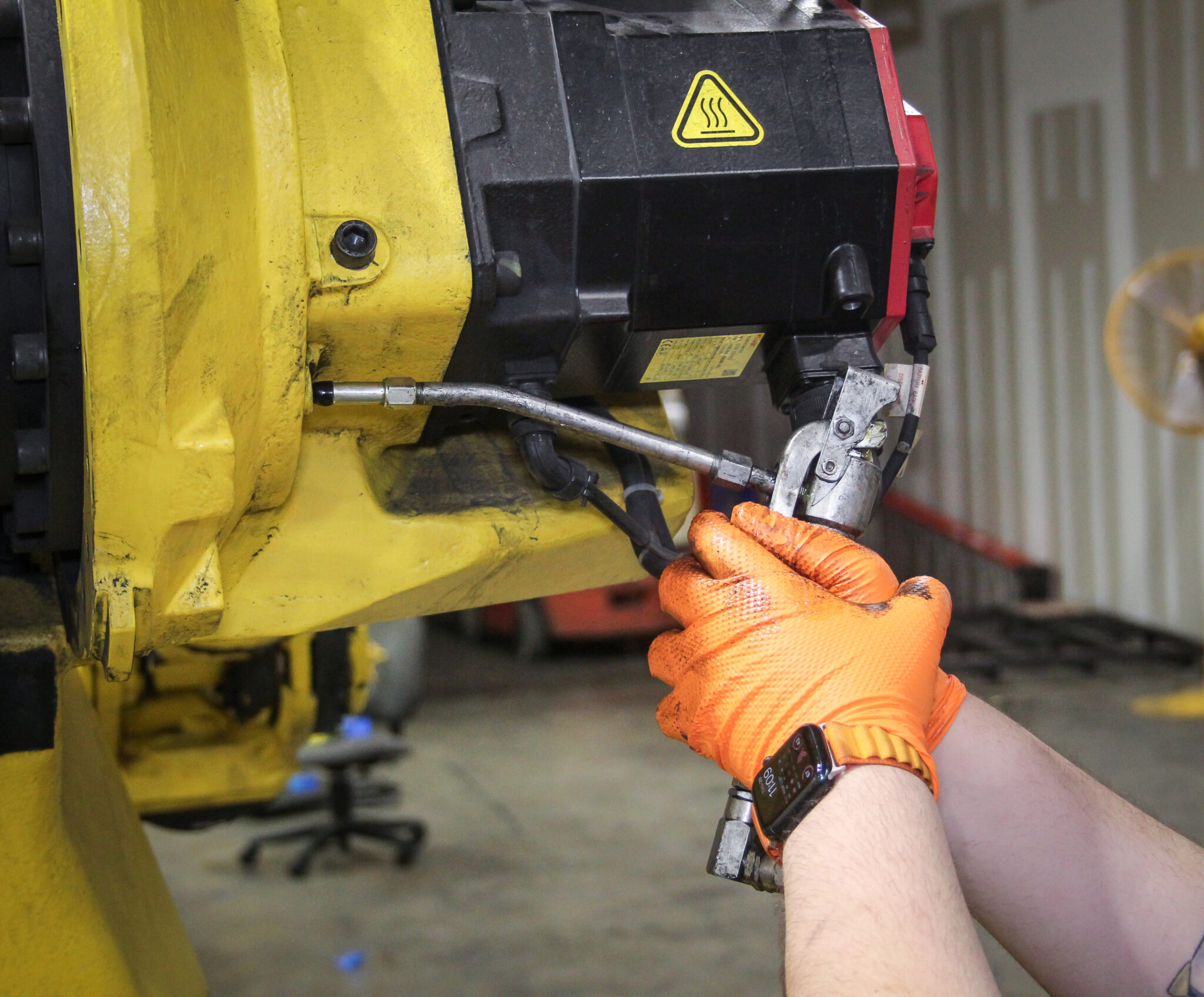
Slipping Through the Cracks: Choosing the Right Grease for Your Industrial Robot
Learn how to identify the best grease for your industrial robots.
Was this helpful?
0 / 0