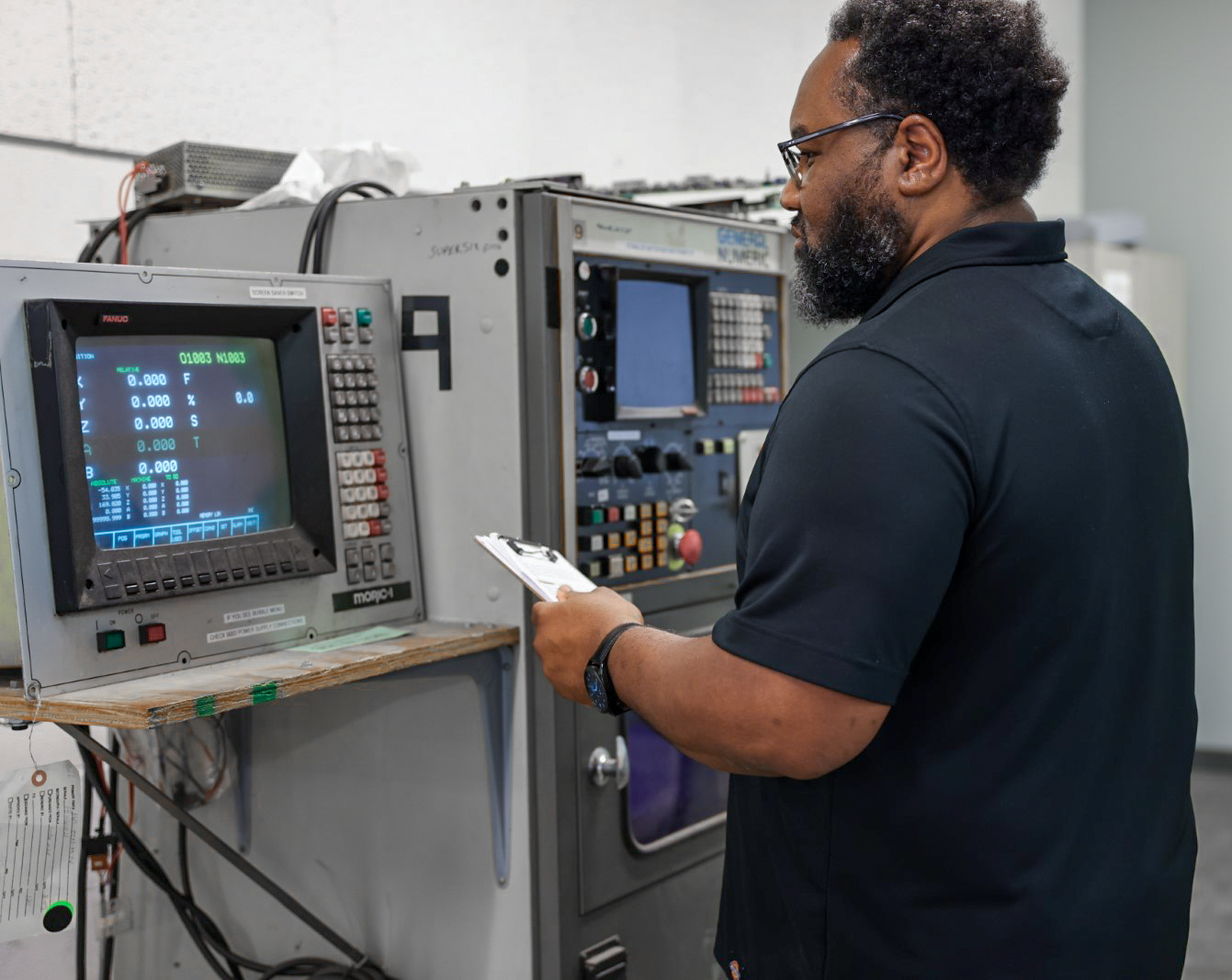
Consumers have intense expectations about the quality, availability, and accessibility of the products they demand. Therefore, in numerous industries, especially those that rely on CNC machine systems, downtime can significantly impact production schedules and profitability. One of the most effective ways to reduce downtime and boost productivity is through comprehensive CNC training to develop the expertise of staff members who use CNC machines. Proper training equips operators with the necessary CNC maintenance skills to troubleshoot issues, optimize machining processes, and perform preventative maintenance, leading to smoother operations and higher output.
The Impact of Operator Errors and Lack of Training
Many CNC machine breakdowns and inefficiencies stem from operator errors and inadequate training. Without proper CNC training, operators may struggle with:
- Incorrect machine setup leading to wasted materials and time.
- Improper tool selection resulting in tool breakage or suboptimal cutting conditions.
- Inability to diagnose machine malfunctions leading to extended downtime and costly repairs.
- Neglecting preventative maintenance that can result in premature wear and tear.
By investing in structured in-person training, manufacturers can empower their workforce, improving uptime and increasing overall efficiency.
Top Ten Critical Reasons for CNC Training
1. Identify and Resolve Issues Quickly.
Trained CNC operators can quickly diagnose and resolve issues like tool breakage, incorrect part dimensions, or machine malfunctions. With the ability to recognize and correct errors efficiently, downtime is minimized.
2. Preventative Maintenance
Routine maintenance is essential for prolonging machine lifespan. CNC training teaches operators how to perform regular inspections and identify potential problems before they lead to failures. This proactive approach helps ensure machines operate at peak performance.
3. Understanding Machine Capabilities
A trained workforce understands the limitations and capabilities of CNC machines. With this knowledge, operators can make informed decisions, avoid excessive wear, and optimize machining parameters for better results.
4. Optimized Machining Processes
Training helps operators learn efficient CNC programming techniques, reducing setup time and optimizing machining parameters for faster cycle times.
5. Material Handling and Tool Selection
Proper material handling and correct tool selection can prevent tool breakage and reduce waste. Training ensures that operators use the appropriate tools for the job, leading to better efficiency and lower costs.
6. Advanced Machining Techniques
Training introduces operators to advanced techniques, including high-speed machining, to increase cutting efficiency and multi-axis machining, which enhance complex part production and improve cycle times.
7. Faster Production Cycles
When CNC operators are well-trained, they can optimize machining processes, leading to shorter production cycles and increased output.
8. Reduced Waste and Scrap
Skilled operators can recognize and avoid common errors, improving material utilization and cost savings.
9. Consistent Quality
CNC training emphasizes the importance of consistent quality control. Well-trained operators ensure that each part meets specifications, reducing rework and defects that can lead to delays.
10. Increased Uptime
By focusing on preventative maintenance and effective troubleshooting, CNC training helps ensure that machines run smoothly and consistently, maximizing uptime and overall efficiency.
Real-World Examples of CNC Training Impact
Example 1: Automotive Manufacturer Reduces Downtime by 30%
A leading automotive manufacturer faced frequent machine stoppages due to operator errors and tool failures. After implementing a comprehensive CNC training program, operators learned:
- How to properly set up CNC machines.
- The importance of preventative maintenance.
- How to troubleshoot common errors quickly.
As a result, the company reduced downtime by 30% and increased output by 20% within six months.
Example 2: Aerospace Company Optimizes CNC Performance
An aerospace company was experiencing delays due to machine programming and material handling inefficiencies. By enrolling their workforce in in-person training, they achieved:
- 25% reduction in setup time.
- Improved material utilization and reduced scrap.
- Enhanced multi-axis machining capabilities, leading to faster production cycles.
Example 3: Small Job Shop Improves Operator Skills
A small CNC job shop struggled with frequent tool breakages and inconsistent part quality. After training operators in:
- Proper tool selection.
- High-speed machining techniques.
- Routine CNC maintenance.
They saw a significant drop in machine breakdowns, resulting in 15% more uptime and 10% higher productivity.
Example 4: Heavy Equipment Manufacturer Reduces Machine Failures
A heavy equipment manufacturer dealing with high failure rates in their CNC-machined components faced costly downtime and repair expenses. After implementing a structured CNC training program, their operators learned:
- How to detect early signs of wear and prevent breakdowns.
- Proper calibration techniques for precision machining.
- Effective troubleshooting methods to resolve machine errors quickly.
As a result, they reduced unplanned downtime by 35% and increased overall equipment effectiveness (OEE) by 22%, leading to more consistent production output and lower maintenance costs.
Example 5: Medical Device Manufacturer Enhances Precision and Reduces Errors
A medical device manufacturer faced challenges with inconsistent part quality and frequent machining errors, leading to increased rework and production delays. After enrolling their CNC operators in specialized in-person training, they achieved:
- 40% reduction in machining errors, leading to higher product consistency.
- 20% decrease in rework, saving valuable production time.
- Improved knowledge of multi-axis machining, allowing for better handling of complex components.
This investment in CNC training improved efficiency and ensured compliance with strict medical industry standards.
How to Access CNC Training
For manufacturers looking to invest in CNC training, several options are available:
- In-Person Training: Hands-on courses like those offered at Fanuc Training Programs provide practical experience for operators.
- Online Courses: Digital resources allow operators to learn at their own pace.
- On-the-Job Training: Working directly with experienced professionals ensures immediate application of skills.
Invest in CNC Training with T.I.E. Industrial
Reducing downtime and increasing productivity in CNC manufacturing starts with proper training. Skilled operators:
- Minimize machine errors and inefficiencies.
- Improve troubleshooting and preventative maintenance.
- Optimize machining processes for better performance.
T.I.E. Industrial is a trusted supplier of refurbished CNC systems, replacement parts, and technical support. We offer comprehensive CNC training solutions to help businesses boost efficiency and reduce costly downtime.
Explore our extensive inventory of supplies and services, especially regarding CNC systems, parts, and training programs today. Contact T.I.E. Industrial to learn how we can help you maximize uptime and productivity.
Was this helpful?
0 / 0