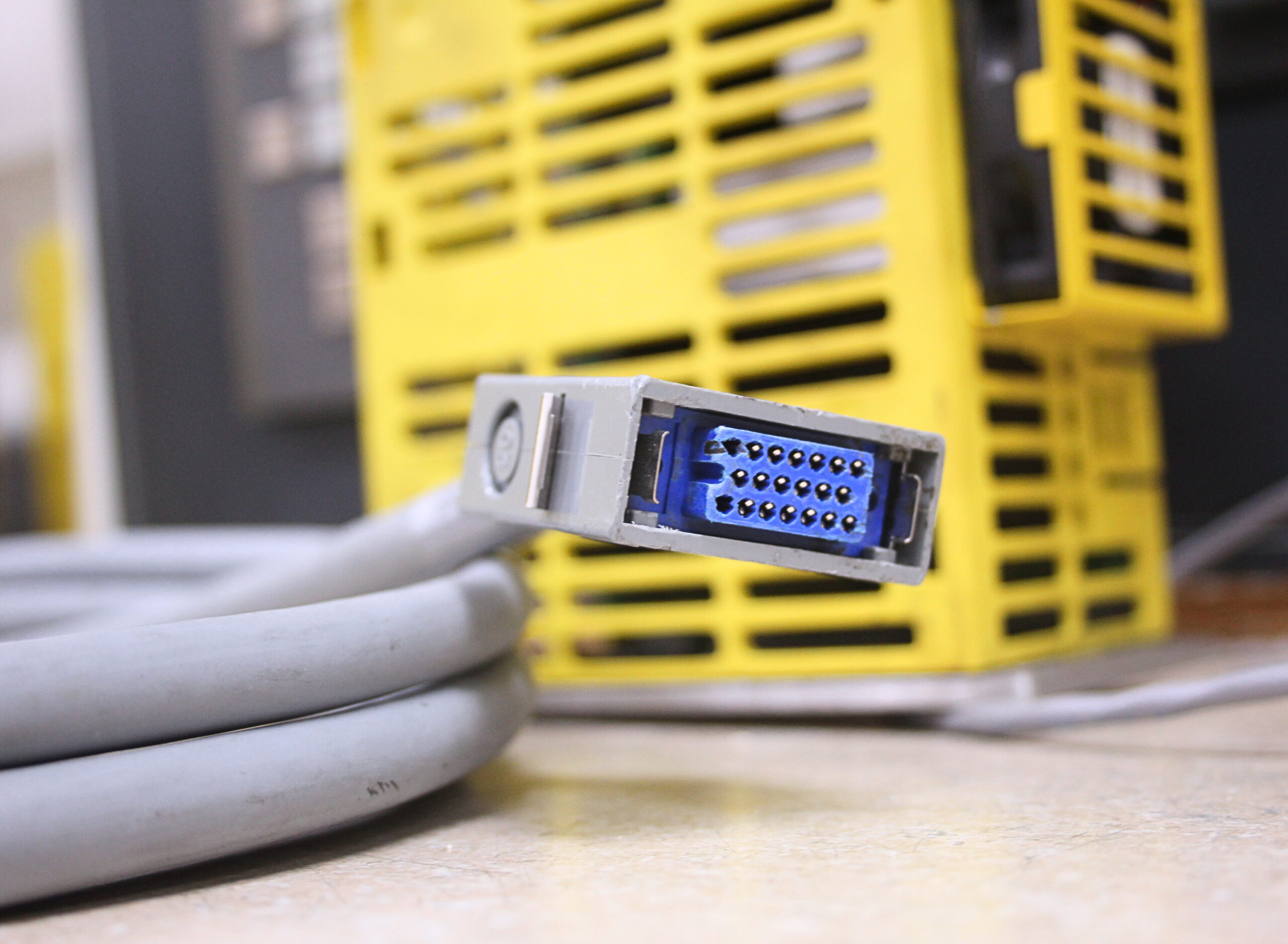
Fanuc motor feedback cables, used in CNC machine (Computer Numerical Control) systems, play a crucial role in the communication between the CNC control unit and the motors, providing a feedback loop that allows the system to monitor and control the motor’s movements accurately.
The use of high-quality and properly functioning CNC motor feedback cables is essential for the accuracy and reliability of CNC machines. Any issues with these cables can result in errors in motor movement, affecting the precision of machining operations. This article will provide information about the functions of these cables and how to address any related issues that may occur during manufacturing operations. Let’s look at some practical solutions to keep your machinery running efficiently.
The Critical Role of Fanuc CNC Motor Feedback Cables
In a CNC machine system, motors drive various components, such as the spindle or the axes of a machine tool. The motor feedback system helps the control unit ensure the motor moves as intended. It typically involves an encoder, which provides feedback on the motor’s position, speed, and direction.
The motor feedback cables transmit signals between the motor and the CNC control unit. These cables carry the feedback signals from the encoder to the control unit, allowing the system to adjust the motor’s operation in real time.
When dealing with Fanuc motor feedback cables, following the manufacturer’s guidelines for installation, maintenance, and replacement is important. Regular inspection and proper handling of cables contribute to the overall performance and longevity of the CNC system.
Common Issues with CNC Motor Feedback Cables
- Cable Damage
Causes. Over time, the motor feedback cables may experience wear and tear due to constant movement, bending, or exposure to harsh environmental conditions. Physical factors like cuts, abrasions, or pressure can lead to cable damage.
Effects. Cable damage can interrupt the communication between the CNC control system and the motor encoder. This disruption can result in inaccurate feedback, causing erratic movements or, in severe cases, complete system failure.
- Connector Problems
Causes. Connectors are critical points in the motor feedback cable system, and issues may arise from repeated plugging and unplugging, poor connections, or damage to the connector pins.
Effects. Faulty connectors can lead to intermittent signal loss, causing instability in the CNC system’s performance. Due to the inconsistent feedback received from the motor, the system may experience sudden stops or unexpected movements.
- Signal Interference
Causes. External factors such as electromagnetic interference (EMI) or radio-frequency interference (RFI) can introduce unwanted signals into the motor feedback cables. This interference may result from nearby electronic equipment, power sources, or other electromagnetic fields.
Effects. Signal interference can lead to inaccuracies in motor positioning information. The CNC control system may receive corrupted feedback signals, impacting the precision of machining operations. This interference can manifest as subtle errors or noticeable deviations in the final machined product.
- Environmental Factors
Causes. Exposure to extreme temperatures, moisture, or chemicals in the working environment can degrade the insulation and overall integrity of motor feedback cables.
Effects. Environmental factors can accelerate wear on the cables, leading to insulation breakdown, corrosion, or other forms of damage. This degradation can compromise the signals transmitted between the motor and the CNC control system, affecting the accuracy and reliability of the CNC machine.
- Installation Errors
Causes. Improper installation, including incorrect routing, excessive tension, or sharp bends in the cables, can contribute to premature wear and damage.
Effects. Incorrectly installed cables may be prone to damage, leading to signal disruptions. Tension or tight bends can cause stress on the cables, impacting their performance over time and potentially causing connection issues.
Diagnosing Fanuc Motor Feedback Cable Issues
Visual Inspection: Regular visual inspection of motor feedback cables is essential for early detection of damage. Look for any signs of wear, cuts, or exposed wires. Promptly replace any damaged cables to prevent further issues.
Connector Checks: Ensure that connectors are securely attached and free from damage. Regularly inspect pins for any signs of wear or deformation. Cleaning connectors and ensuring a snug fit can help prevent intermittent signal loss.
Signal Testing: Utilize diagnostic tools or other testing equipment to measure and analyze the signals transmitted through the motor feedback cables. Identify any irregularities and address them accordingly.
Effective Cable Fixes and Solutions
Cable Replacement. Replacing the motor feedback cable is often the most effective solution in severe damage. T.I.E. Industrial offers a comprehensive range of refurbished Fanuc motor feedback cables, ensuring quality and reliability at a cost-effective price.
Shielding and Grounding. Proper shielding and grounding techniques can be employed to mitigate signal interference. T.I.E. Industrial offers guidance on implementing effective shielding solutions to enhance the performance of your Fanuc motor feedback cables.
T.I.E. Industrial – Your Source for Reliable Fanuc Motor Feedback Cables
Addressing issues with Fanuc motor feedback cables is crucial for maintaining the precision and efficiency of your company’s CNC systems. T.I.E. Industrial can provide high-quality refurbished Fanuc motor feedback cables, ensuring your machinery operates at peak performance. Contact T.I.E. Industrial today to overcome common cable issues and keep your production lines running and producing.
Was this helpful?
0 / 0