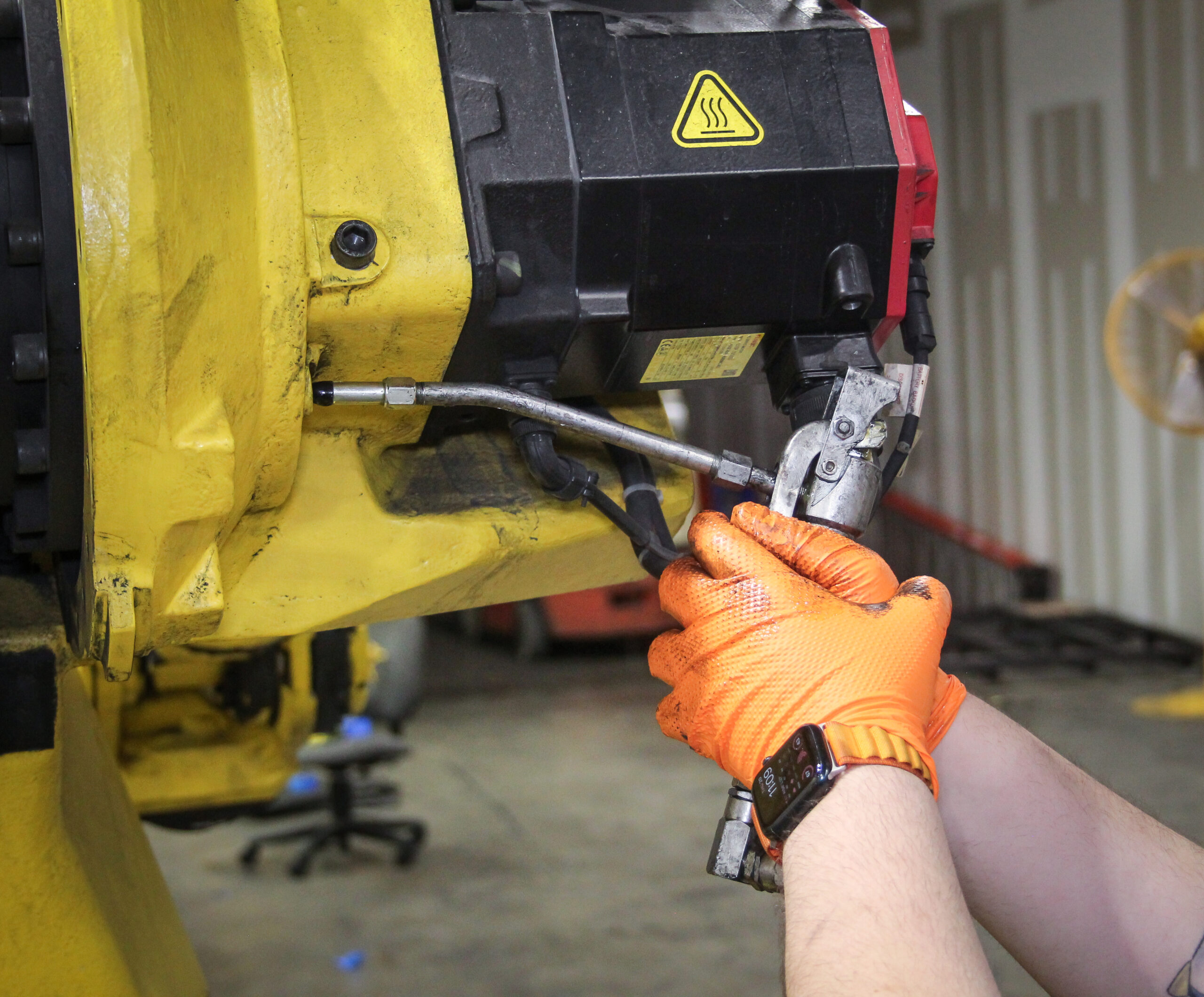
Proper lubrication is the backbone of industrial robot maintenance, ensuring smooth operation, minimal wear, and extended equipment lifespan. Yet, many maintenance teams overlook one critical detail—choosing the right industrial robot grease. Using the wrong grease or neglecting lubrication can lead to premature wear, overheating, and costly breakdowns, reducing efficiency and profitability.
This article will break down the different types of industrial robot grease and explain why OEM-recommended options are essential—helping you keep your robots running at peak performance.
Why Grease Matters in Industrial Robots
Industrial robots operate in high-speed, high-precision environments, where even minor friction can lead to major performance issues. Proper lubrication is essential to keep robotic joints, gears, and bearings functioning smoothly, reducing mechanical resistance and ensuring optimal movement. Grease serves as a protective barrier within robotic systems, preventing metal-to-metal contact in critical areas such as:
- Joints: Reduces friction at rotating and pivoting points, ensuring accurate motion control.
- Gears: Lubricates internal gears to prevent grinding, excessive wear, and performance degradation.
- Bearings: Helps maintain smooth rotational movement while distributing loads evenly across components.
Without the proper industrial robot grease, components experience excessive friction, leading to :
- Heat buildup: Increases the risk of overheating and component failure.
- Wear and tear: Speeds up the degradation of gears and bearings, reducing robot lifespan.
- Contamination risks: Dust, debris, and moisture can infiltrate unprotected parts, leading to corrosion and mechanical malfunctions.
Understanding Different Types of Industrial Robot Grease
Selecting the right industrial robot grease is crucial for maintaining smooth operations and prolonging the life of your robotic system. Below is a breakdown of industrial robots’ most commonly used greases and their key benefits.
1. Lithium-Based Grease
- One of the most commonly used greases in industrial applications.
- Provides excellent lubrication and stability over a wide temperature range.
- Offers good water resistance and oxidation stability.
- Used in general-purpose applications, including robotic bearings and joints.
2. Calcium Sulfonate Grease
- Known for its high load-carrying capacity, making it ideal for heavily loaded robotic components.
- Offers excellent water resistance, making it suitable for environments with high humidity.
- Provides superior protection against rust and corrosion.
3. Polyurea Grease
- Performs well in high-temperature environments, making it commonly used in electric motor applications.
- Offers excellent shear stability to resist breaking down under mechanical stress.
- Compatible with a wide range of materials but requires careful selection to avoid compatibility issues with other grease types.
4. Fluorinated Grease
- Designed for extreme conditions where resistance to harsh chemicals and high temperatures is essential.
- Provides excellent performance in aggressive manufacturing environments.
- Typically used in specialized robotic applications that require non-reactive lubrication.
5. Molybdenum Disulfide (MoS₂) Grease
- Ideal for extreme pressure conditions and is commonly used in high-load robotic gearboxes and joints.
- Forms a solid lubricating film that reduces wear and enhances performance under heavy loads.
- Used in applications where metal-to-metal contact occurs under intense pressure.
Choosing the right industrial robot grease depends on the application and operating environment. Using the wrong grease type can lead to premature wear, overheating, and mechanical failure.
Why You Should Always Use OEM-Recommended Grease
Regarding industrial robot maintenance, using OEM-recommended grease isn’t just a suggestion—it’s a necessity. Every robot manufacturer designs its components to work with specific lubricants, ensuring optimal performance, longevity, and reliability. Choosing the wrong grease can lead to severe mechanical failures, costly repairs, and even voided warranties.
Original Equipment Manufacturer (OEM) grease is rigorously tested to work with specific robot models and their components, including:
- Joints and bearings – Ensures smooth movement and prevents excessive wear.
- Gear systems – Reduces friction while maintaining consistent lubrication under varying loads.
- Seals and gaskets – Prevents chemical degradation that can lead to leaks and failures.
Robot manufacturers like Fanuc, ABB, Motoman, and KUKA specify grease formulations tailored to their machines. Using anything other than the OEM-recommended grease can compromise the robot’s operation and longevity.
While it might be tempting to use a cheaper or more readily available lubricant, the risks far outweigh the short-term savings:
- Chemical Breakdown – Some greases are incompatible with robotic materials, leading to premature degradation.
- Seal and Component Damage – Non-OEM grease may not provide the right viscosity or protection, causing leaks and increased wear.
- Warranty Voidance – Many manufacturers will not honor warranties if improper lubrication is used.
- Reduced Performance – Using the wrong grease can lead to overheating, excessive friction, and component failure.
Manufacturer-Specific Grease Recommendations
Leading industrial robot brands specify unique grease formulations for their machines. Below are some well-known examples:
- Fanuc: Molywhite RE00, Daphne Eponex Grease No. 2
- ABB: Staburags NBU 30 PTM, Mobilgrease 28
- KUKA: Klüberplex BEM 34-132, Klübersynth GE 46-1200
Following manufacturer guidelines ensures the best performance and longevity of your robotic system. Following the OEM-recommended schedule for lubrication is essential, as excessive wear can occur if intervals are too long.
Choosing the Right Grease for Long-Term Robot Performance
Proper lubrication is one of the simplest yet most effective ways to keep your industrial robots running at peak performance. By selecting the right industrial robot grease, following manufacturer guidelines, and maintaining a regular lubrication schedule, you can prevent costly downtime, extend the lifespan of your equipment, and ensure smooth, efficient operation.
Key Takeaways for Robot Maintenance:
✔ Always use OEM-recommended grease to ensure compatibility and optimal performance.
✔ Follow a routine lubrication schedule to prevent excessive wear, overheating, and contamination.
✔ Avoid mixing different grease types, as this can cause chemical instability and reduce effectiveness.
✔ Monitor for signs of lubrication failure, including leaks, abnormal noises, and erratic movement.
Find the Right Grease for Your Industrial Robots
At T.I.E. Industrial, we provide high-quality OEM and aftermarket lubrication solutions to help you keep your robots in top condition. Whether you need Fanuc, ABB, KUKA, or Motoman-approved greases, our team is here to help you find the best products for your equipment.
Contact us today and explore our full range of industrial robot maintenance solutions.
Get your Fanuc CNC machine back up and running.
TIE offers same day shipping on more than 100,000 Fanuc CNC parts in stock. We offer a 1 year in service warranty on all parts and repairs.
Shop PartsWas this helpful?
0 / 0