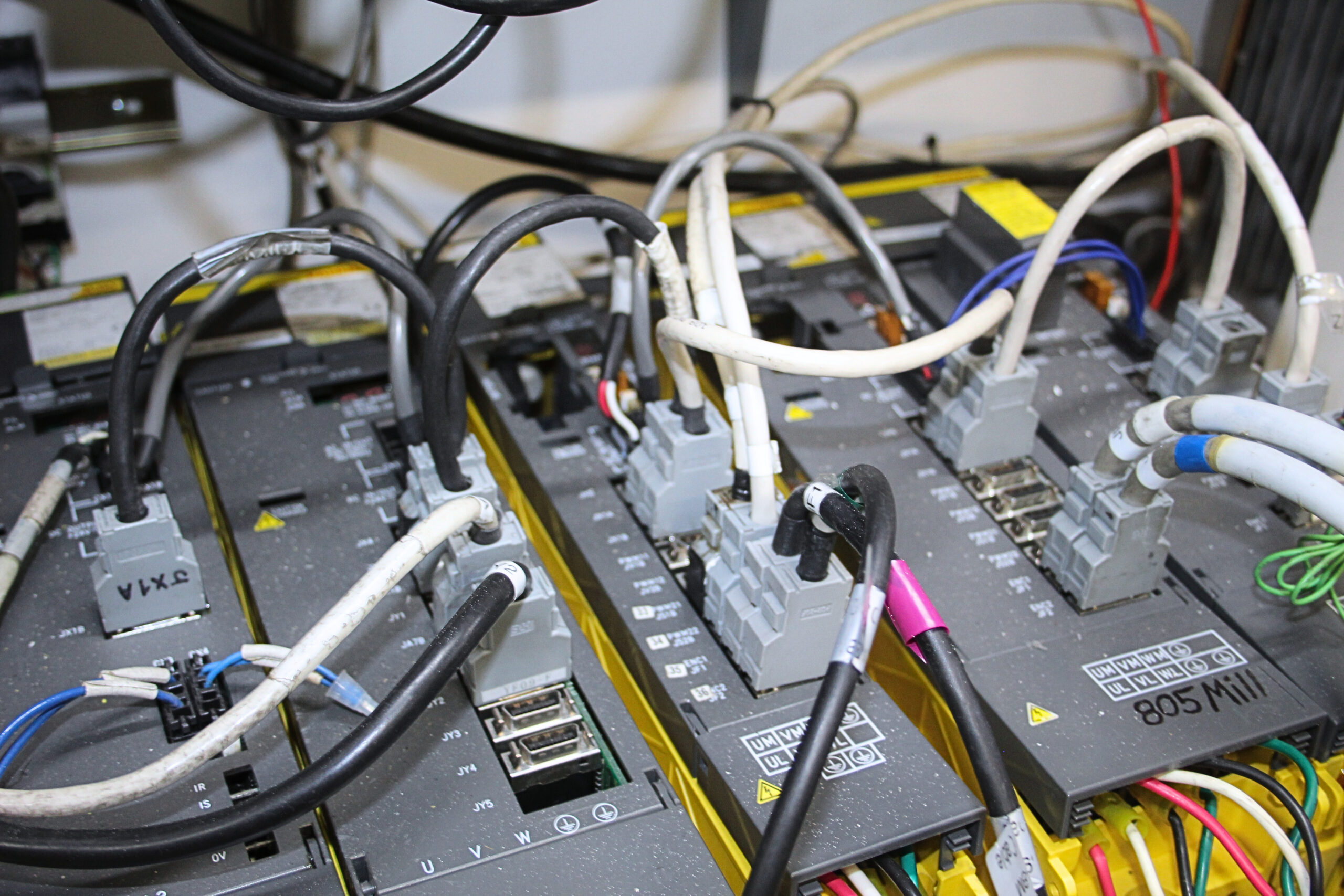
Manufacturers use CNC machines for numerous reasons, as these advanced machining tools offer advantages to improved functionality, efficiency, repeatability, precision, increased production speed, and flexibility in the manufacturing process.
Having a well-maintained and fault-free CNC system is crucial. One common challenge CNC operators face is detecting cable faults within the Fanuc CNC machine systems. Let’s examine the necessity of identifying and addressing cable faults to ensure your operations run seamlessly.
The ABCs of CNC Machine Systems
Before diving into the specifics of cable fault detection, let’s briefly understand the significance of Fanuc CNC systems. The CNC machine system refers to a manufacturing system in which computerized controls and programming are used to operate and control the movements of machine tools across many industries. Renowned for their cutting-edge technology and reliability, Fanuc systems power countless manufacturing processes worldwide. CNC machines follow pre-programmed instructions to cut, shape, and manipulate materials such as metal, plastic, wood, or composites, offering efficiency, consistency, and high levels of precision in the manufacturing process.
Clusters of Cables: Your CNC Machine Connections
Cables are an integral component in CNC machines, serving several crucial purposes:
- Data Transmission. Cables facilitate the transmission of data between CNC machine system components. This includes communication between the computerized control unit, motor drives, sensors, and other peripheral devices. Data cables ensure the accurate and timely exchange of information, allowing for precise control over the machine’s movements.
- Power Distribution. In CNC machines, various motors and components require electrical power to operate. Power cables distribute electrical energy from the power source to these components, ensuring the machine’s functionality. Proper power distribution is essential for reliable and efficient operations.
- Single Transmission. CNC machines rely on sensors and feedback devices to monitor and control different aspects of the machining process. Signal cables transmit signals between these sensors and the control unit, providing real-time tool position, speed, and accuracy feedback.
- Control and Command Connections. Cables establish connections between the CNC control unit and the various machine elements. These connections enable the execution of programmed instructions, allowing the CNC machine to follow specific toolpaths, speeds, and sequences, playing a vital role in ensuring that the machine operates according to the set parameters.
- Emergency Stop and Safety Features. Specialized cables are often integrated into CNC machines for emergency stop functions and safety features. These cables enable the rapid shutdown of the machine in case of emergencies, ensuring operator safety and preventing potential damage to the equipment.
- Feedback Loop for Closed-Loop Systems. Censors are instrumental in CNC machines with closed-loop systems, where real-time adjustments are made based on feedback. These cables transmit feedback signals from sensors to the control unit, allowing the system to make dynamic corrections to maintain accuracy and consistency during machining.
- Flexibility and Movement. Cables are designed to be flexible and durable, accommodating the dynamic movements and rotations of various machine components. This flexibility is essential in CNC machines, where tools and workpieces may move in multiple axes during the machining process.
Common Cable Faults in Fanuc Systems
Cable faults can manifest in various forms, from minor disruptions to severe malfunctions. Recognizing these faults early on can prevent costly downtimes and maintain the productivity of your operations. Here are some common cable faults encountered in Fanuc CNC systems:
- Intermittent Connectivity Issues. These can disrupt the seamless communication between different components. These faults often result from damaged cables, loose connections, or wear and tear. Regular inspections are crucial to identify and rectify these issues promptly.
Models that can be affected: Fanuc Series 0, 16, 18, 21
- Short Circuits and Open Circuits. Short circuits and open circuits can occur due to damaged insulation or broken wires within the cables. This can lead to erratic behavior or complete system failure. Understanding the cable configurations specific to your Fanuc model is essential for effective troubleshooting.
Models that can be affected: Fanuc Series 30, 31, 32, 35
- Faulty Power Supply Cables. Power supply cables are vital for ensuring a steady flow of electricity to the CNC system. Faults can result in voltage fluctuations, causing instability in the system. Regular checks on power supply cables are imperative to maintain optimal performance.
Models that can be affected: Fanuc Series 0i, 16i, 18i, 21i
Detecting Cable Faults: A Step-by-Step Guide
Now that we’ve identified common cable faults let’s look at detecting and addressing these issues:
- Visual Inspection. Begin with a thorough visual inspection of all cables connected to the Fanuc CNC system. Look for signs of wear, fraying, or damage. Pay close attention to cable connectors and ensure they are securely attached.
- Multimeter Testing. Utilize a multimeter to measure the continuity of cables. This involves checking for any breaks or interruptions in the flow of electrical current. Be sure to refer to the specifications of your Fanuc model for accurate testing parameters.
- Insulation Resistance Testing. Perform insulation resistance testing to identify potential short circuits or open circuits within the cables. This test helps in pinpointing areas where the insulation may be compromised.
- Voltage Testing. Verify the voltage levels across power supply cables to ensure they meet the specified values for your Fanuc model. Deviations from the recommended voltage can lead to performance issues and system instability.
In conclusion, the ability to detect and address cable faults in Fanuc CNC systems is a skill that every professional in the manufacturing industry should possess. By following the steps outlined in this guide and staying vigilant with regular inspections, you can ensure the uninterrupted performance of your Fanuc CNC systems, including all cables.
T.I.E. Industrial is committed to providing high-quality refurbished Fanuc CNC parts to support your maintenance efforts and keep your operations running smoothly. Trust us as your dedicated partner in the world of Fanuc CNC solutions.
Get your Fanuc CNC machine back up and running.
TIE offers same day shipping on more than 100,000 Fanuc CNC parts in stock. We offer a 1 year in service warranty on all parts and repairs.
Shop PartsWas this helpful?
0 / 0